Makita Magnetic Drilling Machine HB350 Instruction Manual
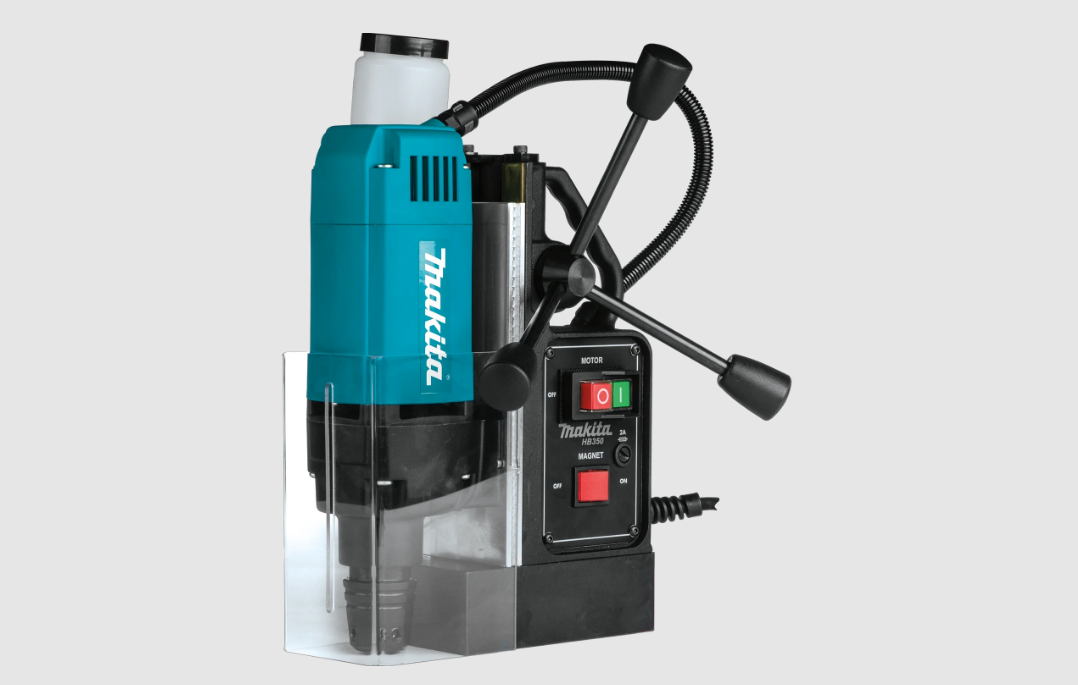
Content
Makita Drilling Machine Introduction
The Makita Magnetic Drilling Machine HB350 is a robust tool designed for precision drilling in steel, capable of cutting holes up to 1-3/8 inches in diameter and 2 inches thick. Featuring a powerful 10-amp motor that operates at 850 RPM, it ensures efficient performance in various applications. Its lightweight design enhances portability and ease of use, making it ideal for tight spaces. The current price for the HB350 is approximately $1,199, reflecting its industrial-grade capabilities.
HB350 MOTOR PARTS
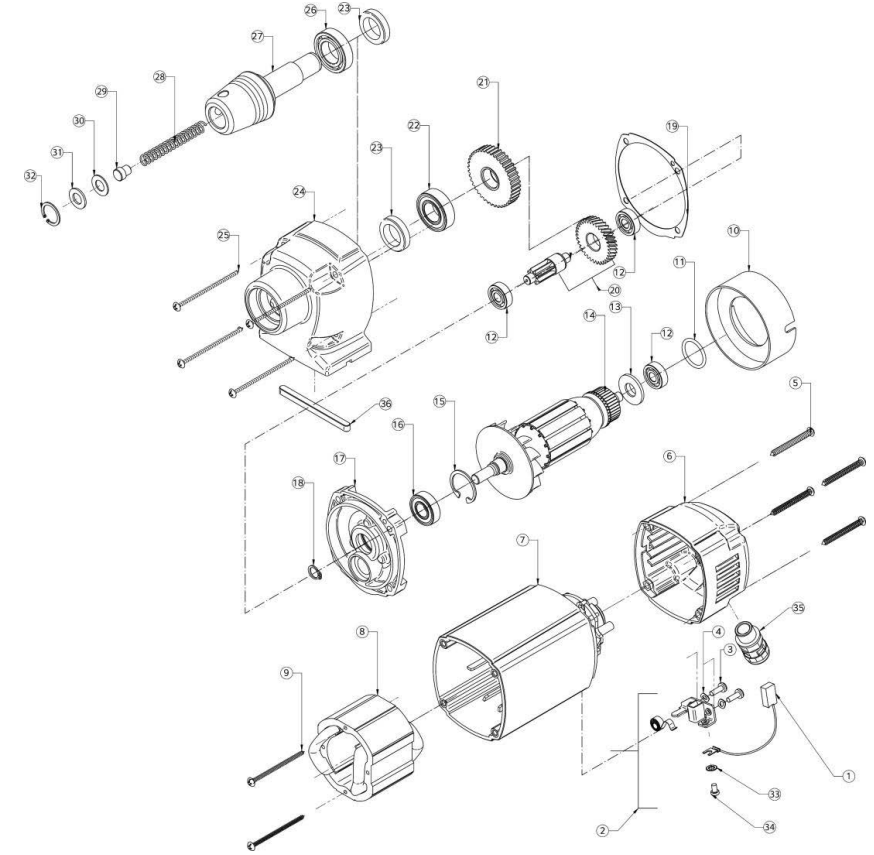
Nr. | Description | Qty | Part No |
1 | CARBON BRUSH IS ASSY. 6.3X10X18 | 2 | EBD002 |
2 | BRUSH HOLDER ASSY. | 2 | EBD001 |
3 | SCREW M4 X 12 | 2 | EBD003 |
4 | SPRING WASHER M4 | 2 | EBD004 |
5 | PHILIPS HEAD SELF-TAP SCREW 4.8X45 | 4 | EBD005 |
6 | BACK COVER | 1 | E1B527 |
7 | FIELD COIL CASING | 1 | E1B526 |
8 | FIELD COIL ASSY 110V | 1 | EBD008-A |
FIELD COIL ASSY 230V | 1 | EBD008-B | |
9 | PHILIPS HEAD SELF-TAP SCREW 3.9X60 | 2 | EBD009 |
10 | BAFFLE | 1 | EBD010 |
11 | 0 RING | 1 | EBD011 |
12 | BALL-BEARING (8-22-7) 608 2Z | 3 | UDCO22 |
13 | DUST WASHER | 1 | EBD012 |
14 | ARMATURE ASSY 110V | 1 | EBD013-A |
ARMATURE ASSY 230V | 1 | EBD013-B | |
15 | CIRCLIP 28MM X 1.2 B TYPE | 1 | EBD014 |
16 | BALL BEARING (12-28-8) 6001 2Z | 1 | UDCO23 |
17 | GEARCASE COVER | 1 | EBD015 |
18 | CIRCLIP 10MM X 1 A TYPE | 1 | EBD016 |
19 | GASKET | 1 | EBD017 |
20 | INTER SHAFT ASSY. | 1 | EBD018 |
21 | SPINDLE GEAR | 1 | EBD019 |
22 | BALL BEARING (17-35-10) 6003 2RS | 1 | UDC004 |
23 | OIL SEAL 20-30-7 B TYPE | 2 | EBD020 |
24 | GEARCASE | 1 | EBD021 |
25 | PHILIPS HEAD SELF-TAP SCREW 4.8 X 60 | 4 | EBD022 |
26 | BALL-BEARING 6904 2RS | 1 | EBD025 |
27 | ARBOR BODY. | 1 | EIB528 |
28 | ARBOR SPRING | 1 | EBD026 |
29 | ARBOR EJECTION PLUG | 1 | EBD027 |
30 | ARBOR WASHER | 1 | EBD028 |
31 | ARBOR RUBBER WASHER | 1 | EBD029 |
32 | ARBOR CIRCLIP | 1 | EBD030 |
33 | CARBON BRUSH WASHER | 2 | EBD031 |
34 | CARBON BRUSH FIXING SCREW | 2 | EBD032 |
35 | PG9 PUSH-FIT GLAND | 1 | 40025 |
36 | MOTOR LOCATING KEY | 1 | M1019 |
STAND PARTS
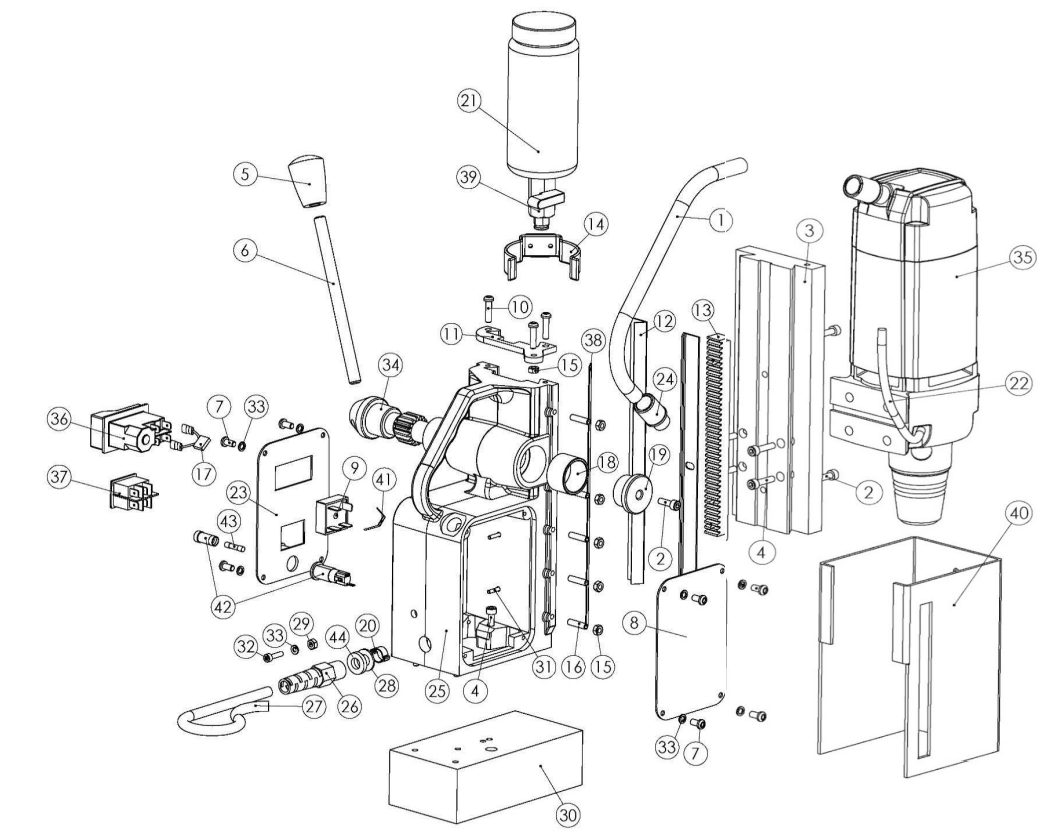
Nr. | Description | Qty | Part No |
1 | CONDUIT (large dia 12mm) – PMA-PCLT-10B.50 | 1 | M0443 |
2 | M6 X 16 CAP HEAD SCREW | 3 | SC616CAP |
3 | SLIDE HB350 MAKITA | 1 | M1000 |
4 | M6 X 25 CAP HEAD SCREW | 7 | SC625CAP |
5 | HANDLE KNOB (10mm KNOCK ON) | 3 | M0841 |
6 | 10MM X 130MM HANDLE (SMALL) | 3 | BD043 |
7 | M4 X 6 BUTTON HEAD SCREW | 8 | SC46BUT |
8 | WARNING PLATE MAKITA HB350 CE JAPAN | M1002 | |
WARNING PLATE MAKITA HB350 CE BELGIUM | M1003 | ||
WARNING PLATE MAKITA HB350 CSA JAPAN | M1014 | ||
WARNING PLATE MAKITA HB350 UKCA UK | M1018 | ||
WARNING PLATE MAKITA HB350 RCM AUSTRALIA | M1021 | ||
9 | 25A – BRIDGE RECTIFIER (395-4310) | 1 | M0401 |
10 | M5 X 16 CAP HEAD SCREW | 3 | SC516CAP |
11 | OILFEED TOP BRACKET – (MB30 BODY) | 1 | M0811A |
12 | BRASS RAIL (MB30) | 2 | M0101 |
13 | RACK (MB30) | 1 | M0831 |
14 | OIL CUP RETAINING CUP COMPLETE | 1 | 10076C |
15 | M5 NYLON | 6 | 10085B |
16 | M5X25 KNURLED POINT GRUB SCREW | 5 | 10085A |
17 | CAPACITOR | 1 | RD43118 |
18 | BUSH (PINION) – 33 X 28 X 20 OIUTE BUSH | 2 | M0081 |
19 | PINION END CAP – DEEP | 1 | M0072 |
20 | 0 CLIP 8-11 BOCUP8/11 | 1 | RD47179 |
21 | D5000 OIL CUP ASSEMBLY | 1 | 30046A |
22 | u-06040(30MC) 6MM X 4MM CLEAR POLYURETHANE TUBE | 1 | BD029 |
23 | MAKITA HB350 CONTROL PANEL PLATE | 1 | M1001 |
24 | M16 PUSH FIT GLAND – PMA BVND-M160GT | 1 | 40026 |
25 | MB30 BODY BLACK | 1 | M0001BLK |
26 | M16 PIGTAIL GLAND COMPLETE WITH LOCK NUT – BBSM 16 | 1 | 10231 |
27 | USA CABLE -14 GAUGE – 3M – AB-CAB-870 | CABLO3 | |
EUROPEAN CABLE C/W MOULD PLUG – AB-CAB-876 – 3M | CABLO4 | ||
MAKITA BRAZIL CABLE C/W PLUG 220V – 3M | CABLO5 | ||
3MTR-11W MAINS LEAD BLACK C/W IND PLUG | CABLO6 | ||
ARGENTINA CABLE C/W PLUG – 230V – 3M | CABLO8 | ||
AUS/NZ-3M MAINS CABLE C/W MOULDED PLUG-AB-CAB-866 | CABLO9 | ||
28 | M8 WASHER FOR ARBOR INTERNAL | 1 | RD47187 |
29 | M4 BRASS NUT | 1 | N UT-M4-B |
30 | HB350 MAGNET BASE | 1 | M1020 |
31 | M4 X 6 SLOTTED CSK MC SCREW – BZP | 5 | SC46CSK |
32 | M4 X 12 CSK MC SCREW – BRASS | 1 | SC412CSK-B |
33 | M4 SHAKE-PROOF WASHER-BZP-WSH-227-004-ZC221 | 9 | SPWR-M4 |
34 | PINION – (SMALL) | 1 | M0041 |
35 | EIBENSTOCK BHM35 DRILL UNIT – 110V MAKITA BLUE | EIB522 | |
EIBENSTOCK BHM35 DRILL UNIT – 230V MAKITA BLUE | EIB523 | ||
36 | DRILL STOP/START SWITCH – 110V- KJD17F/120V/50HZ – | NCP001 | |
DRILL STOP/START SWITCH – 230V- KJD17F-230V-50HZ- | NCP002 | ||
37 | MAGNET SWITCH – NCP PANEL – B418CG00000 | 1 | NCP006 |
38 | G.F.S. (MB30) | 1 | M0441 |
39 | 1/8 BSP-6MM BLACK PUSH FIT | 1 | 50015 |
40 | GUARD TO SUIT NEW UNI 1 MBQ35N/EQ35N/EBM35 | 1 | VISO18 |
41 | 318-565 VARISTOR (V150LA10A) | W18XC522 | |
VARISTOR HIGH SURGE 20MM 275 VRMS | W18XC521 | ||
42 | 248-447 FUSE HOLDER | 1 | W18XC511 |
43 | 2A FUSE (RAPID 26-2469) | 1 | W18XC512 |
44 | WASHER SMBK1869836HPU | 1 | U0D009 |
Detailed Specifications
- Motor Power: 750W high-torque motor for efficient drilling.
- Magnetic Base: Strong neodymium magnet with 4,400 lbs. of holding force.
- Speed Control: Adjustable speed (100-450 RPM) for optimal performance.
- Drilling Capacity: Up to 2 inches (50 mm) with twist drills and 3 inches (76 mm) with annular cutters.
- Weight: Approximately 44 lbs. (20 kg) for easy handling.
- Cooling System: Built-in cooling system to prolong tool life.
BEFORE YOU START
To help you get the best possible performance from your new Magnetic Drilling Machine, this guide contains simple, sensible pointers for the safe, effective, and long-term use of the equipment. Please read it carefully before using the drill. Ensure that you have observed all the general and specific safety procedures.
Explanation of the pictograms on the specification plate of the Makita HB350
![]() | DANGER! Indicates an imminent danger or risk to life and health of a general nature. |
![]() | ELECTRICAL DANGER! This means a direct pending danger or risk to life due to electricity. |
![]() | CAUTION! Indicates a possible danger or risk of slight injury or damage to property. |
![]() | WEAR EYE & EAR PROTECTORS Always wear eye and ear protection when using this drill. |
![]() | USE A SAFETY CHAIN! For safety reasons securely attach the tool to the workpiece. |
![]() | READ THE MANUAL Read the manual before operating the machine. |
Description
The Makita Magnetic Drilling Machine HB350 features a robust design that combines power and precision. The 750W motor delivers high torque, making it capable of handling demanding drilling tasks. The strong neodymium magnetic base ensures stable operation on metal surfaces, while the adjustable speed control allows for flexibility in different drilling applications. The machine is also equipped with a built-in cooling system to enhance tool longevity and performance.
The ergonomic design and balanced weight distribution make it comfortable to use over extended periods. Additionally, the HB350 comes with various safety features, including an emergency stop function and overload protection, ensuring safe operation in demanding environments.
FUNCTIONAL DESCRIPTION
- Cutter capacity – 1.3/8”
- Chuck Capacity – ½”
- No load speed – 850 rpm
- Power consumption – 1050w
- Clamping force – 8000N (1800lb)
- L x H x W – 8.7/8” x 19.5/16” x 7.11/16” Weight – 26lb
- Voltage – 120v
INCLUDES: Integral coolant system, Warranty, Carrying case, Allen keys, Safety strap & Guard.
Due to our continuing program of research and development, these specifications are subject to change without notice.
THE BROACH CUTTING CONCEPT
If you are unfamiliar with the use of annular (or broaching) cutters, take a few minutes to read this guide – you will benefit from the better performance and longer life of the tool if you understand the concept. Annular cutters only cut material at the periphery of the hole, rather than converting the entire hole to shavings. As a result, the time and energy required to make the hole is lower than for a traditional twist drill. The broaching capacity of a machine is, therefore, greater than the twist drill capacity. The slug ejected after the cut also has a higher scrap value than shavings.
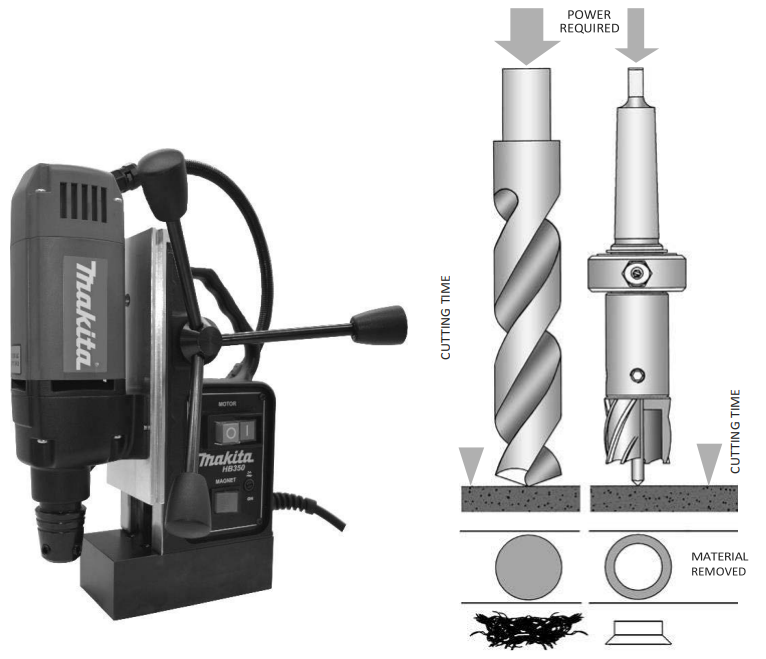
GENERAL POWER TOOL SAFETY INSTRUCTIONS
INTENDED USE
The intended use of this magnetic drill is to drill holes in ferrous metals. The magnet is used to hold the drill in place whilst the drill is functioning. It is designed for use in fabrication, construction, railways, petrochemical, and any other applications when drilling ferrous metal.
Any deviation from its intended use will not be covered by warranty.
GENERAL SAFETY RULES
WARNING! Read and understand all instructions. Failure to follow all instructions listed below may result in electric shock, fire, and/or serious personal injury.
SAVE THESE INSTRUCTIONS.
Work area
- Keep your work area clean and well-lit. Cluttered benches and dark areas invite accidents.
- Do not operate power tools in explosive atmospheres, such as in the presence of flammable liquids, gases, or dust. Power tools create sparks that may ignite dust or fumes.
- Keep bystanders, children, and visitors away while operating a power tool. Distractions can cause you to lose control
Electrical safety
- Grounded tools must be plugged into an outlet properly installed and grounded in accordance with all codes and ordinances. Never remove the grounding prong or modify the plug in any way. Do not use any adaptor plugs. Check with a qualified electrician if you are in doubt as to whether the outlet is properly grounded. If the tools should electrically malfunction or break down, grounding provides a low resistance path to carry electricity away from the user.
- Avoid body contact with grounded surfaces such as pipes, radiators, ranges, and refrigerators. There is an increased risk of electric shock if your body is grounded.
- Don’t expose power tools to rain or wet conditions. Water entering a power tool will increase the risk of electric shock.
- Do not abuse the cord. Never use the cord to carry the tools or pull the plug from an outlet. Keep cord away from heat, oil, sharp edges, or moving parts. Replace damaged cords Damaged cords increase the risk of electric shock.
- When operating a power tool outside, use an outdoor extension cord marked” W-A” or” W”. These cords are rated for outdoor use and reduce the risk of electric shock.
Personal safety
- Stay alert, watch what you are doing, and use common sense when operating a power tool. Do not use tools while tired or under the influence of drugs, alcohol, or medication. A moment of inattention while operating power tools may result in serious personal injury.
- Dress properly. Do not wear loose clothing or jewelry. Contain long hair. Keep your hair, clothing, and gloves away from moving parts. Loose clothes, jewelry, or long hair can be caught in moving parts.
- Avoid accidental starting. Be sure the switch is off before plugging in. Carrying tools with your finger on the switch or plugging in tools that have the switch on invites accidents.
- Remove adjusting keys or switches before turning the tool on. A wrench or a key that is attached to a rotating part of the tool may result in personal injury.
- Do not overreach. Keep proper footing and balance at all times. Proper footing and balance enable better control of the tool in unexpected situations.
- Use safety equipment. Always wear eye protection. Dust mask, non-skid safety shoes, hardhat, or hearing protection must be used for appropriate conditions.
Tool use and care
- Use clamps or another practical way to secure and support the workpiece to a stable platform. Holding the work by hand or against your body is unstable and may lead to loss of control.
- Do not force tool. Use the correct tool for your application. The correct tool will do the job better and safer at the rate at which it is designed.
- Do not use the tool if the switch does not turn on or off. Any tool that cannot be controlled with the switch is dangerous and must be repaired.
- Disconnect the plug from the power source before making any adjustments, changing accessories, or storing the tool. Such preventive safety measures reduce the risk of starting the tool accidentally.
- Store idle tools out of reach of children and other untrained persons. Tools are dangerous in the hands of untrained users.
- Maintain tools with care. Keep cutting tools sharp and clean. Properly maintained tools, with sharp cutting edges, are less likely to bind and are easier to control.
- Check for misalignment or binding of moving parts, breakage of parts, and any other condition that may affect the operation of the tool. If damaged, have the tool serviced before using. Many accidents are caused by poorly maintained tools.
- Use only accessories that are recommended by the manufacturer for your model. Accessories that may be suitable for one tool, maybe come hazardous when used on another tool.
Service
- Tool service must be performed only by qualified repair personnel. Service or maintenance performed by unqualified personnel could result in a risk of injury.
- When servicing a tool, use only identical replacement parts. Follow instructions in the Maintenance section of this manual. Use of unauthorized parts or failure to follow Maintenance Instructions may create a risk of electric shock or injury.
WARNING!
Always use a safety chain. Mounting can release.
MAINTENANCE
- Occasionally apply a few drops of oil to the rack toothing.
- The bearings of the feed shaft are self-lubricating and must not be greased.
- Grease the sliding surface of the carriage with MOLYCOTE grease.
- When not in use or being transported the unit should be kept in the case supplied.
- After use ensure the unit is clean of swarf and dirt.
- Parts that are worn or damaged should be replaced immediately with genuine manufacturer’s replacements.
- Ensure all cutting edges are sharp when in operation. Using blunt cutting tools may lead to an overload of the motor.
- After every 30 minutes of running, it is recommended that the machine is laid on its side to permit grease to run across the gear train.
- After repeated use, the cradle may become loose. This is remedied by adjusting the tension screws on the side of the body. Put 2.5mm hex wrench into the head of the cradle retaining nuts, using an 8mm Spanner undo the locking nuts anti-clockwise, holding the hex wrench without moving grub screws. Using the hex wrench gently tighten screws in series until the cradle moves freely in the slide but does not allow the motor to wobble. When adjustment is complete re-tighten locking nuts clockwise, ensuring the grub screws do not move from their new position
IMPORTANT! – TO PREVENT DAMAGE TO THE CIRCUITRY, NEVER USE ELECTROMAGNETIC DRILLING MACHINES AND WELDING EQUIPMENT ON THE SAME WORKPIECE SIMULTANEOUSLY.
Optional Accessories
For details of options, either refer to the catalog or inquire at the store of purchase or a Makita sales office.
CAUTION: These accessories or attachments are recommended for use with your Makita tool specified in this manual. The use of any other accessories or attachments might present a risk of injury to persons. Only use accessory or attachment for its stated purpose.
If you need any assistance for more details regarding these accessories, ask your local Makita Service Center.
- HSS Cutter
- TCT Cutter
- Drill chuck
MATERIAL AND CUTTING SPEEDS
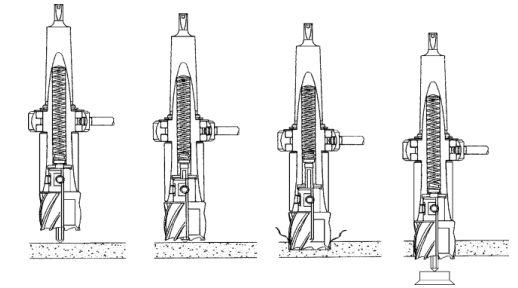
- The ease with which material can be drilled is dependent on several factors including tensile strength and abrasion resistance. Whilst hardness and/or strength is the usual criterion, wide variations in machinability can exist among materials showing similar physical properties.
- The cutting conditions can be dependent upon requirements for tool life and surface finish and further restricted by the rigidity of the tool and workpiece, lubrication, and machine power available.
- The harder the material the slower the cutting speed. Some materials of low hardness contain abrasive constituents leading to rapid cutting-edge wear at high speeds. Feed rates are governed by the rigidity of set up, the volume of material to be removed, surface finish, and available machine power.
- It is preferable to set and maintain a constant surface speed (RPM) for a given material and vary the feed rate within defined limits.
- Machine feed is measured in inches or millimeters per minute and is the product of RPM x number of teeth in the cutter x feed per tooth. Too light or excessively high feed rates will both cause premature cutter failure. Heavy feeds on hard materials will cause chipping of the cutting edge and excessive heat generation.
- Slender and long-shanked cutters are restricted in feed rate due to deflection, and wherever possible the largest and most robust tool must be used.
This is important for harder materials. Steel up to 400 HB is the potential limit for conventional M2 HSS tools. Above 300 HB, cobalt alloy cutters should be considered for increased tool life. In softer grades of material, cobalt alloy cutters may give increased output by increasing speeds and feed rates by up to 50%. Tungsten Carbide cutters permit surface speeds and feed rates up to those for standard cutters.
FEEDS AND SPEEDS
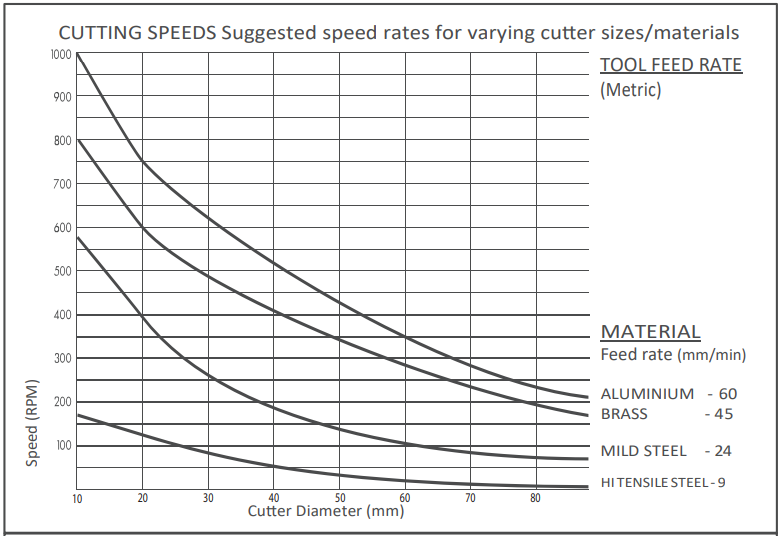
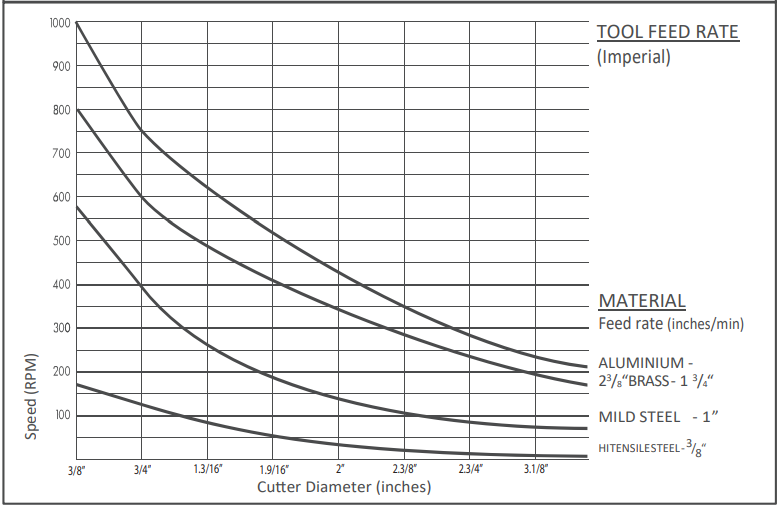
PLEASE NOTE: These figures are quoted as a starting point. Actual performance will be dictated by material type, thickness and hardness, application, and cutter condition.
FITTING THE SAFETY GUARD
DRILL GUARD INSTRUCTIONS
Ensure the drill unit is isolated from the power supply.
Fit guard to drill as shown.
When drilling, the guard should always be in contact with the surface being drilled. As the drill is lowered, the guard will rise in relation to the drill.
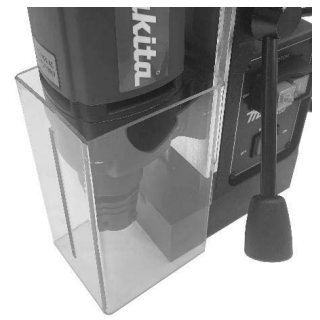
FITTING THE OIL BOTTLE
The cutting oil bottle is held in a sprung bracket attached to the top of the drill body. Fit the bracket by removing one of the cap screws from the top plate and replacing the bolt through the fixing lug on the bottle bracket, tightening the bolt enough to allow some radial movement of the bracket. The coolant tube is a push-fit into the self-seal gland at the base of the tap and a similar fitting on the lower arbor bracket.
FITTING THE SAFETY CHAIN
A safety chain should be used wherever possible as a safety precaution in the event of a power failure releasing the magnet; particularly in situations where the machine is clamped onto a vertical surface or in an inverted position.
SAFETY CHAIN INSTRUCTIONS
When the machine has been clamped to the workpiece in the correct position for drilling, the chain should be fitted at a secure part of the drill. Then passed around a substantial part of the workpiece and fastened securely.
Once the cut is complete, the chain should be released, and the machine supported before the magnet is disengaged.
FITTING THE CUTTER
Insertion of pilot pin
The pilot pin is used to both centers the cutter and eject the slug on completion of the cut. It has a flat side to allow coolant to run down to reach the center of the cut where the heat is greatest. Slide the pin through the hole in the center of the cutter shank.
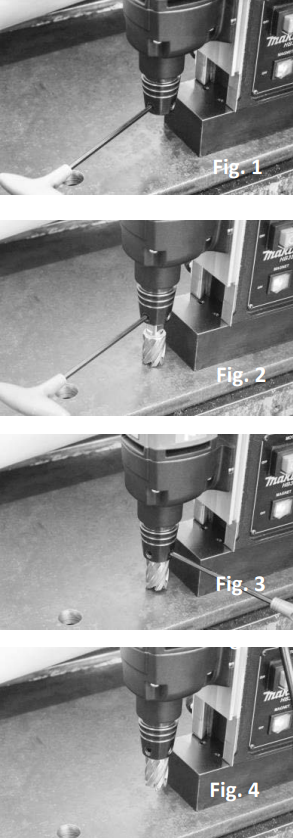
- Fig 1.
To insert the cutter in the arbor, first loosen the grub screws, using an M5 hexagonal wrench. Ensure the grub screws are sufficiently loose enough to allow the shank of
the cutter to enter freely. - Fig 2.
Ensure the drive flats on the cutter shank are fully aligned with the two grub screws in the machine arbor. - Fig 3.
Ensuring the shank of the cutter is fully inserted inside the arbor, tighten the grub screws fully to give the cutter a secure fitting inside the arbor. - Fig 4.
The cutter is now ready for use.
APPLYING COOLANT
- Cutting oil ensures longer cutter life and enables the slug to be ejected cleanly. A 500 ml bottle is included with every machine.
- Oil will be automatically delivered to the cutter when the cut commences.
- When cutting on vertical surfaces or upside down, cutting paste, gel or foam is recommended. It is best applied inside the cutter before drilling.
- Plug the machine into the power socket and the red LED on the electronic control panel will flash.
N.B. The safety strap and guards have been omitted from the photos for clarity.
OPERATION
Power Ensure power to the drill and that the drill is safe to operate.
Magnet ON To turn the magnet ON or OFF, use the magnet switch as pictured.
Motor ON Press the GREEN Switch to turn the motor on. Proceed with cutting – following all safety guidelines.
Motor OFF To stop the motor press the RED switch. The motor will stop and the magnet will remain on. Go back to step 3 to start over.
Setup Guide
To operate the Makita Magnetic Drilling Machine HB350,
- Start by ensuring the work surface is clean and free from debris.
- Place the magnetic base on the metal surface and engage the magnet by flipping the switch.
- Once securely attached, attach the drill bit or annular cutter to the spindle.
- Set the desired speed using the speed control dial and begin drilling slowly while maintaining steady pressure.
- For assembly, ensure all components are securely fastened according to the manufacturer's instructions.
- Configuration involves setting up the machine according to your specific drilling needs, including adjusting the speed and ensuring proper cooling system operation.
Troubleshooting
Common problems with the Makita Magnetic Drilling Machine HB350
- Including inadequate magnetic adhesion, overheating, and improper drill bit alignment.
- To address these issues, ensure the work surface is clean and dry before engaging the magnet.
- Regularly check and maintain the cooling system to prevent overheating. Always align drill bits properly to avoid damage to both the tool and workpiece.
- Important instructions and warnings include ensuring proper safety gear is worn during operation, such as safety glasses and gloves.
- Avoid using the machine near flammable materials or in hazardous environments.
Makita Magnetic Drilling Machine HB350 Pros & Cons
Pros
- High Torque Motor: Efficient for heavy-duty drilling operations.
- Strong Magnetic Base: Provides stable operation on metal surfaces.
- Adjustable Speed Control: Flexibility in different drilling applications.
- Ergonomic Design: Comfortable use over extended periods.
- Safety Features: Emergency stop function and overload protection for safe operation.
Cons
- Weight: Heavy machine requiring careful handling.
- Cost: Higher price point compared to smaller drilling machines.
- Maintenance: Requires regular maintenance of cooling system and magnetic base.
Customer Reviews
The Makita Magnetic Drilling Machine HB350 has received positive reviews from professionals and serious DIY enthusiasts alike. Many users praise its powerful motor and strong magnetic base, which provide stable and efficient drilling operations. However, some users have noted the high price point and the need for regular maintenance as potential drawbacks.
A common complaint is the weight of the machine, which can make it difficult to maneuver for extended periods. Despite this, the overall consensus is that the HB350 is a reliable and high-performance tool suitable for demanding drilling tasks.
Faqs
What is the recommended usage of the Makita Magnetic Drilling Machine?
How do I ensure proper magnetic adhesion with the Makita Magnetic Drilling Machine HB350?
What safety features does the Machine HB350 have?
Why does my Makita Magnetic Drilling Machine overheat during operation?
How do I assemble and configure the Magnetic Drilling Machine?
How do I maintain the cooling system of my Makita Magnetic Drilling Machine HB350?
Can I drill through thick metal with the Machine?
Is the Makita Magnetic Drilling Machine ergonomic?
Leave a Comment