Sovans Electric Pallet Stacker CTD10R-E | Operating Guide
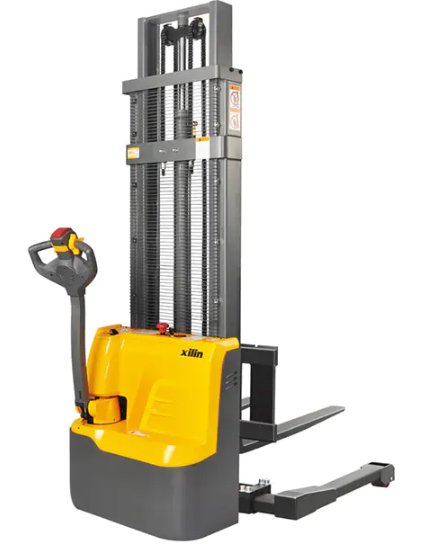
Content
Introduction of Sovans Electric Pallet Stacker CTD10R-E
Say hello to the Sovans Electric Pallet Stacker CTD10R-E, a game-changer in material handling! This powerful machine is designed to transport and stack goods efficiently, making it an essential tool for warehouses, factories, and retail stores. With an estimated price range of $3000 to $4000 and a launch date set for Q2 2023, the CTD10R-E is poised to redefine productivity and safety in the industry.
Lists of Accessories, Spare Parts, and Vulnerable Parts
CTD10RE Accessories, Spare Parts, and Vulnerable Parts
No. | Name | Use Position | Type & Specification | Quantity | Remarks |
---|---|---|---|---|---|
1 | Key to the electric lock | Unlock the electric lock | 2 | ||
2 | Fuse | Electric equipment | 50A | 1 | |
3 | Fuse | Electric equipment | 125A | 1 | |
4 | Sealing ring | Oil cylinder | UHS4 | 1 | |
5 | O type sealing ring | Oil cylinder | 50X3.55 | 1 | |
6 | Composite ring | Oil inlet of cylinder | D14 | 1 | |
7 | Dustproof ring | Oil cylinder | DH40 | 1 | |
8 | O type sealing ring | Oil cylinder | UHS40 | 1 |
Structure Diagram (Explosion Diagram) and Principle Diagram of the Major Parts
See attached diagram I for "The principle diagram of hydraulic system"
- See Electric Instructions for "Instruction of the electric system"
See attached diagram II for “The explosion diagram”
Packing List
Packing List of CTD10RE Electric Pallet Stacker
No. | Name | Quantity | Net Weight | Dimension (L×W×H) | Remarks |
---|---|---|---|---|---|
1 | CTD10RE electric pallet stacker | 1 | A complete set. | ||
2 | Accessory box | 1 | Technical documents, accessories and spare parts. |
Note
- The following documents are in the file:
- Operation manual of CDDR Electric Pallet Stacker (1 volume)
- Packing list (1 copy)
- Qualification certificate (1 copy)
- Accessories and spare parts:
No. | Name | Use Position | Type & Specification | Quantity | Remarks |
---|---|---|---|---|---|
1 | Key to the electric lock | Unlock the electric lock | 2 | ||
2 | Fuse | Electric equipment | 50A | 1 | |
3 | Fuse | Electric equipment | 125A | 1 | |
4 | Sealing ring | Oil cylinder | UHS4 | 1 | |
5 | O type sealing ring | Oil cylinder | 50X3.55 | 1 | |
6 | Composite ring | Oil inlet of cylinder | D14 | 1 | |
7 | Dustproof ring | Oil cylinder | DH40 | 1 | |
8 | O type sealing ring | Oil cylinder | UHS40 | 1 |
Powered Industrial Trucks Safety Code
Safety Code of Motor Industrial Trucks in Service, Operation, and Maintenance
Detailed Specifications
Key features of the Sovans Electric Pallet Stacker CTD10R-E include a 1000 kg load capacity, 120-degree steering, and an adjustable fork length of 550 - 1150 mm. The powerful 24V 200Ah battery provides long-lasting performance, while the ergonomic design ensures comfortable operation. Additional specifications include:
- Travel speed (load/no load): 6/9 km/h
- Lifting speed (load/no load): 0.3/0.5 m/s
- Lifting height: 2100 mm
- Chassis width: 680 mm
- Ground clearance: 80 mm
Warning!
Operators must strictly conform to ISO3691 "Safety Specifications of Motor Industrial Vehicles”. Untrained personnel are not allowed to operate the stacker.
According to ISO 3691 “Safety Specification of Motor Industrial Vehicles”, load capacity and lifting height of our CDD Electric Pallet Stacker are stipulated as follows:
- When the lifting height of CTD10R-E stacker is below 2500mm (including2500mm), the maximum load capacity is the rated capacity. Overloading is prohibited.
When the lifting height of CTD10R-EIII stacker is above 2500mm (excluding2500mm), the load capacity is less than the rated bearing capacity. Take the following diagrams as a reference with the rated loads of 1000kg.
Brief introduction
CDDR electric pallet stacker adopts storage batteries as the dynamic source and a AC motor as the driving force, traveling through gear transmission. The lifting of the fork relies on the DC motor and the hydraulic transmission system. The up-and-down movement of the oil cylinders lifts the fork and the goods. As the traveling and lifting of the stacker are electrically driven, it possesses the characteristics of energy saving, high efficiency, stable operation, safety and reliability, low noise and no pollution, etc. This stacker adopts 24V storage battery, which greatly prolongs use time after one charging.
The stacker is applicable for goods piling and handling on hard and flat ground.
Allowed environment for using:
- Height above sea level shall not be over 1000m;
- Ambient temperature shall not be higher than +40℃ and no lower than -25℃;
- When the ambient temperature reaches +40℃, the relative humidity should not exceed 50%; at a lower temperature, higher relative humidity is allowed.
- Hard and flat ground.
- It is prohibited to use the stacker in a flammable, explosive or corrosive environment with acid and alkali.
Description
The instruction manual shall be kept by the operator, and shall be read by the operator until he gets a full understanding.
The instruction manual is composed of correct operation, convenient and simple maintenance, and routine inspection. The instruction manual shall be carefully read before operation, for purpose of correct drive and suitable maintenance to ensure safe and effective material transportation. The instruction manual may be in disagreement with practical product due to product innovation. The instruction manual shall be based on the actual operation and data transfer. The instruction manual can be supplemented with in case of truck leasing or transfer.
Description of symbol: Regulations of the following symbols are of great importance to your safety and others as well.
Please observe these regulations
- Danger: Indicates an impending danger. Deaths or severe injuries would be resulted without any precaution or avoidance. You must observe those requirements.
- Warning: Indicates a potential danger. Deaths or severe injuries would be resulted without any precaution or avoidance. You must observe those requirements.
- Caution: Indicates a potential danger. Moderate injuries would be resulted without any precaution or avoidance. You must observe those requirements.
- Notice: You shall pay attention to statements that are in direct or indirect relation with personal security and truck maintenance.
Outline drawing
CTD10R-E Outline drawing
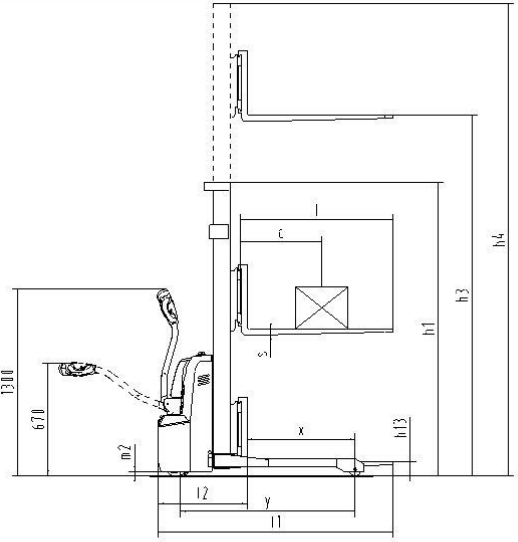
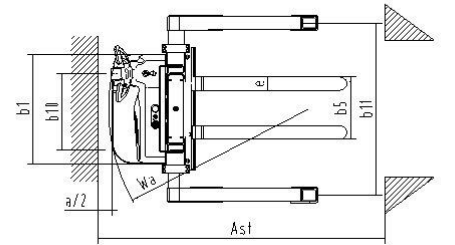
CTD12R-E Electric Pallet Stacker
Characteristic | Value |
---|---|
Manufacturer (abbreviated) | |
Model | CTD10R-E |
Driving model | Electric (Storage battery) |
Driving model | Walking |
Rated load (Q) kg | 1000 |
Load center distance (C) mm | 500 |
Front overhang (X) mm | 720 |
Tread (B) mm | 700 |
Service weight (with battery) kg | 1250 |
Axle load, front/rear, laden | 515/705 |
Axle load, front/rear, unladen | 500/750 |
Wheel dimension, front | Ø 250 x 75 |
Wheel dimension, rear | Ø 80 x 70 |
Additional wheel dimension | Ø 140 x 50 |
Wheel number, front/rear | 1x / 1x + driving wheel |
Tread, front (B1) mm | 900 |
Tread, rear (B2) mm | 160 |
Height of mast, lowered (H1) mm | 2100 |
Free lift (H2) mm | 150 |
Lifting height (H3) mm | 3000 |
Height of mast, extended (H4) mm | 3800 |
Height of overhead guard (H5) mm | 2250 |
Overall length (L1) mm | 1720 |
Length to fork face (L2) mm | 1800 |
Overall width of truck body (B3) mm | 1125 |
Fork dimension (S/E/L) mm | 40/100/1200 |
Wheelbase (Y) mm | 1200 |
Turning radius (Wa) mm | 1650 |
Travel speed, laden/unladen (Km/h) | 5/5.5 |
Lifting speed, laden/unladen (m/s) | 0.1/0.12 |
Lowering speed, laden/unladen (m/s) | 0.3/0.25 |
Battery voltage, capacity (V/Ah) | 24/105 |
Battery weight (kg) | 300 |
Sound level at operator's ear (dB(A)) | 70 |
Safety Norms
Warning
- This electric truck is only limited to utilization indoor with a hard flat floor. Operation in inflammable, explosive environment or corrosive environment such as acid or alkaline condition shall be strictly forbidden.
- Only drivers who have received formal training or are authorized are allowed to operate the stacker; check the truck whether it is in its normal condition before operation.
- Read this instruction carefully before operation so as to master the performance of the stacker; check the truck whether it is in its normal condition before operation.
- Overloading operation is forbidden.
- As for goods carrying and operation, center of gravity of the goods must be within the range of the two forks. It is strictly forbidden to transport loose goods.
- The truck shall travel slowly when forks pass in or out of pallet.
- It is strictly forbidden to transport goods by lowering button during the traveling of the truck. Meanwhile, switch off the truck when lowering button is rapidly or frequently, because rapid and frequent lifting or lowering will lead to damage on the truck and goods.
- Don't load heavy goods on the truck for a long time.
- Don't lay goods on the forks during transport.
- It is strictly forbidden to make sharp turn on narrow aisle. When it is turning, slow down the truck so as to ensure the safety of persons nearby.
- Do not exceed the first speed limits when the forks are lifted.
- It is strictly forbidden to transport goods by lifting heavy goods and forks.
- This kind of electric stacker is only limited to utilization indoor with a hard flat floor.
- Operation in inflammable, explosive environment or corrosive environment such as acid or alkaline condition shall be strictly forbidden.
- Only maintenance personnel with the same training or authorization are allowed to repair or replace parts.
- Use suitable pallet. The pallet shall be of suitable dimensions, neither too wide nor too large.
Notice
- Even though each electric pallet stacker may have the same technical parameters, there may be differences on features of braking and acceleration as well. Never drive the truck until you get familiar with all those operations.
- Please put on safety shoes and protective clothes. Do not wear clothes that are too loose for sake of being caught, which would result in danger.
- Never drive the truck when you are tired or un-concentrated, with an injection of drug, or after a liquor drinking.
Warning: Do not make modifications on the truck.
- Please observe safety rules and regulations of your working place during operation, inspection, and maintenance of the truck.
- Unauthorized truck modification is not permitted.
- No modifications or alterations to a powered industrial truck, which may affect, for example, capacity, stability or safety requirements of the truck, shall be made without the prior written approval of the original truck manufacturer, its authorized representative, or a successor thereof. This includes changes affecting, for example, braking, steering, visibility and the addition of removable attachments. When the manufacturer or its successor approve a modification or alteration, they shall also make and approve appropriate changes to capacity plate, decals, tags and operation and maintenance handbooks.
- Only in the event that the truck manufacturer is no longer in business and there is no successor in the interest to the business, the user may arrange for a modification or alteration to a powered industrial truck, provided, however, that the user shall: a) Arrange for the modification or alteration to be designed, tested and implemented by an engineer(s) expert in industrial trucks and their safety; b) Maintain a permanent record of the design, test(s) and implementation of the modification or alteration; c) Make appropriate changes to the capacity plate(s), decals, tags and instruction handbooks; d) Affix a permanent and readily visible label to the truck stating the manner in which the truck has been modified or altered together with the date of the modification or alteration, and the name and address of the organization that accomplished the tasks.
Notice
- Before checking the electrical system, turn off the key switches and the emergency isolation switches.
- Before starting up the truck, please ensure that there is no person around it.
Notice
If the driver’s view is shielded by the bulky goods carried, please drive backwards or drive under the guidance of other working personnel.
Notice
Ensure no people around the truck when driving backwards.
Notice
Driving through the narrow access shall be guided by working personnel.
Notice
At crossroad or other places impeditive for view, the driver shall not drive until there is no person at both sides.
Notice
Keep concentration when operating truck.
Caution
The driving mechanism of truck is installed on the foreside. Due to this difference from common vehicles, the foreside of truck swings comparatively fast when turning around. For this reason, to prevent collision with other objects nearby the foreside of truck, do drive or turn slowly.
Strictly forbid harsh driving
Notice
Never start up, brake or turn abruptly. Abrupt start-up or braking may cause the falling of goods.
Notice
Abrupt turning during traveling may cause the tilting of truck and result in serious accident. Do decelerate and take care to turn.
Notice
Observe all items of safety rules on working place. Decelerate and sound horn when travel by other truck or vehicles. Avoid driving in places with bad view.
Notice
Ensure to provide certain clearance between truck and entrance.
Notice
Ensure to provide enough distance between the truck and roadside or platform edge. When running on narrow road or platform, keep a certain safety distance with the edge against falling of the truck.
Warning
Avoid turning or loading and unloading operation on slope; otherwise the truck can go tilting.
Operation norms
Notice
The truck can only carry goods under rated capacity.
- Forbid overloading operation.
- Forbid defective transportation.
- Passengers on the truck must be forbidden.
- Never push or pull the truck by vehicle.
- Never use the truck as lifting appliance.
- When transporting and stacking goods, the driver shall be extremely careful to turn slowly to keep balance of the goods. Do start, turn and descent, meanwhile, watch around for sake of safety.
- The faulty truck for future repair must not be parked at places impeditive for traffic. Lower down the fork and turn the key switch to the OFF position.
- The grounding wire of truck must not be removed.
- Take care to avoid the danger of wind force when loading goods.
Notice
Take care to avoid the danger of wind force when loading goods.
- The operator shall master the traveling speed according to site condition. The truck shall slow down and move at a low speed when turning, at a narrow aisle, passing by swing doors or places where view impeded. And the truck shall keep enough distance with the forklift moving forward. Abrupt stop, sharp turn and overtaking are forbidden at dangerous places or where view is impeded except accidents. It is forbidden hold body or hands out of the driving cabin.
- Driver’s view during operating: The driver’s view must keep in the traveling direction of the stacker and pay attention to the surrounding roads at all times. If the goods carried impend the driver’s view, goods carried must be adjusted to the backward of driver’s view. If the goods can not be adjusted, another operator shall be arranged at both sides of the stacker so as to report the forward road condition for the truck driver.
- Upgrade and downgrade driving: The route of upgrade and downgrade shall be specified driving roads. The ground shall be kept clean, safe and reliable in accordance with technical performance of the stacker. When the truck is moving upgrade with goods, the forks should be held in the forward position. While driving downgrade, the stacker shall move backward. Turning, tilting and parking is not allowed during upgrade and downgrade moving. Make sure to slow down when downgrade driving and always make prepare for braking.
- Driving the stacker to elevator or charging platform: When it is necessary to drive the stacker to elevator or charging platform, make sure that elevator or charging platform has enough loading capacity, with the design structure applicable for bearing stacker. Meanwhile the elevator and charging platform should be permitted by the equipment user. Checks must be carried out before operation. Before driving into the elevator, the goods should be elevated to the elevator first and select the suitable parking space for the truck in order to avoid collision with walls during lifting. When there is other person needs to use the elevator, they should place the stacker at first. Then they can come into the elevator afterwards. When the elevator reaches the special height, the personnel shall get out of the elevator at first.
- Conditions of goods to be transported: The stacker operator should check the goods carefully make sure that there is not any risk. Before transportation of the goods, place and locate the goods. If there is any possibility of falling or losing during the goods transportation, it should be mounted with protective devices (such as protective guard).
Important notice after operation
- Parking: Park the truck at appointed place. Never park the truck on slope. Ensure the following points to be achieved before leaving away the truck: a. Lower down the fork to the lowest position naturally. b. Turn off the key switch. c. Turn off the key switch. d. Turn off the key switch.
Notice
When cleaning up the electrical system, use compressed air but not water.
Warning
Open flame is forbidden to appear at the charge places, otherwise, explosion or fire disaster can be caused. Make a record of charge. As for the charge matters referred, refer to the part about storage battery operation.
Initial operation
Initial operation
In case of dangerous conditions, the power can be cut off, and the battery plug must be connected to the emergency parking plug of the stacker itself.
Warning
- It is strictly forbidden to operate the stacker without emergency parking plug.
- The stacker can only be driven by the battery power, but without rectified AC current which may lead to serious damages of the truck. And length of battery cable (tow cable) shall not be over 6m.
- If the stacker is driven by the external battery through a tow cable, it is forbidden to lift the loads.
- Before initial operation of the stacker, checks must be carried out as follows:
Check that whether the device is complete or whether the status is normal.
If the stacker has not been mounted with battery, it must be mounted with battery. Take care not to damage the battery cable. - The feature curve of charger shall be adjusted (charging curve).
- If the truck is not used for a long time, wheels placed on the ground will be pressed. Only after the truck is put into operation for a short time, the wheel can come to the original shape.
Drive of the stacker without the driver of the stacker itself
Warning: It is strictly forbidden to drag the stacker on the slope.
In case of dragging stacker during emergency operation, the electromagnetic brake must be loosened. 2.2 When the stacker is placed at a specified place, the electromagnetic brake must be relocated so as to make the stacker in a state of brake.
Use and operation instruction
The electric pallet stacker adopts storage batteries as the dynamic source for short distance goods handling and stacking. Correct use and operation will bring great convenience to your work but incorrect use and operation will damage the stacker or pose risk to you and your goods.
Warning
It is strictly forbidden to use faulty truck.
- Before operation, please check if the truck is in normal condition: Is there any oil leakage in the hydraulic pipes? Are the supporting wheels at the operate normally? Is there any damages of the truck? Is there any other problems?
Check if there is any electric power in the batteries with the method indicated in Fig.I. Pull the general power switch out to turn on the general power supply, unlock the electric lock on the handle, check the electric energy meter on the instrument panel of the truck. If the zero end grid is bright, it indicates there is no electric power in the batteries and charging should be conducted at once. It is prohibited to operate the truck without electric power as that will greatly reduce the service li fe of the batteries and even damage the batteries.
Check if the truck brake is normal. Check the lifting, dropping, forward and backward traveling of the truck to see if the actions are normal. Check if the emergency reverse action of the truck is normal with the method indicated in Fig.II:
Warning: It is strictly forbidden to turn the accelerator knob fastly to speed up the stacker abruptly during goods transportation.
Move the control handle to division A or division C as indicated in Fig.II and press the rise/lowering button on the control handle to see if the lifting and lowering of the fork is normal. Then turn the control handle to division B as indicated in Fig. II, slowly start the truck and press the handle to the horizontal position to check that whether the truck can travel and brake normally. Move the control handle to division B as indicated in Fig.II, press the emergency reverse button on top of the control handle to ckeck that whether the truck can travel backward normally. After the above check, if there is no failure in the truck, it can be put into operation; if there is some failure, please repair it at once. It is prohibited to use trucks with problems.
In operation
Accelerator knob: The accelerator knob is used for controlling traveling direction and speed of the stacker. When it is for the traveling operation, turn the operation handle to B area indicated in the above diagram. When the handle is in A or C area, the stacker is in a power-off status, and can not travel. When the operation handle is in B area and the accelerator knob is turned in one direction, the stacker wil travel in that direction. While the accelerator is turned in another direction, the stacker will travel in another direction. Meanwhile the bigger the turning amplitude is, the faster the truck will travel.
Note: A side-magnetic brake is installed on the shaft end of the driving wheel motor and there is a cam and an inching switch installed on the rotary shaft of the rotary arm. Only when the rotary arm is at 45°±35°(as indicated in Fig. II), the stacker can be turned on and travel. Larger or less than the angle, the stacker will be powered-off and braked. In that case, the stacker can lift goods. When lifting goods, the stacker cannot travel. As indicated in Fig. II, when the operation handle is in division A or division C, the stacker can only lift or lower but not travel; when the control handle is in division B, the stacker can travel as well as lift or lower. The operation position of the handle will not be specially described in the following descriptions, i.e. the stacker can only lift or lower but not travel when the handle is in division A or C and the handle must be in division B when the stacker is traveling.
As indicated in Fig. II, there is a button on the operation handle which is used for slowing down the stacker. When this “slow down” button is pressed as well as accelerate knob is turned, the stacker will travel at a low speed. This state is best suitable for turning a corner, stacking and moving into and out of the shelf while taking goods. When the “slow down” button is released and the accelerate knob is turned, the stacker will travel at a normal speed.
Safety height: The safety lift height for mast is about 1.8m (according to the assembled mast): If the mast is lifted to a height which is over the safety height, the stacker will slow down to about 3km/h.
Operation of handling and stacking
Notice
Please check the following items before operation of the stacker: Ensure no goods falling and goods damaged at loading and unloading area. Ensure no goods or objects impeding for safety.
As indicated in Fig. II1, pull out the general power supply switch, unlock the electric door lock, and drive the stacker to the goods shelf nearby. (The tip of the fork is 300mm from the goods shelf), press the lowering button, adjust the height of the fork to a proper position, and insert the fork slowly and as deep as possible into the pallet of the goods. Press the lifting button to lift the goods till the bottom of the pallet is 10mm from the goods shelf. Slowly drive the stacker and slowly move the fork away from the shelf (the tip of the fork is 300mm from the goods shelf). Attention should be paid to that there should be no obstracles around and when turning, the speed should be reduced.
Caution: The driving mechanism of truck is installed on the foreside. Due to this difference from common vehicles, the foreside of truck swings comparatively fast when turning around. For this reason, to prevent collision with other objects nearby the foreside of truck, do drive or turn slowly.
Operation of taking goods off the goods shelves
As indicated in Fig. II, pull out the general power supply switch, unlock the electric door lock, and drive the stacker to the goods shelf nearby. (The tip of the fork is 300mm from the goods shelf). Press the lowering button, adjust the height of the fork to a proper position, and insert the fork slowly an d as deep as possible into the pallet of the goods. Press the lifting button to lift the goods till the bottom of the pallet is 100mm from the goods shelf. Slowly drive the stacker and slowly move the goods out of the shelf (the tip of the fork is 300mm from the goods shelf). Press the lowering button and the fork lowers to a height of 200 300mm from the ground. Drive the stacker away from the goods shelf until it reaches a desired position and then slowly stop it. Press the lowering button to put down the goods, make the fork completely away from the goods and move the fork slowly out of the goods pallet.
Abnormal situation handling during operation
- When pressing the lifting button, the fork can rise but when releasing the lifting button, the fork is still rising. The stacker is in a state of lifting control. In that case, turn off the general power supply switch to cut off the power at once. Drive the stacker to a safe position to lower the fork manually and repair the circuit of the stacker.
- If the brake is out of function when the stacker is in operation, the operation must be stopped at once and the general power supply switch must be turned off.
- If you feel that the stacker is moving forward and pushing the operator against a wall or other objects, press the emergency reverse action on the top of the operation handle and the stacker will automatically move backward by itself to avoid injury to the operator.
After operation: After operation, the stacker should be parked in a fixed parking position and routine maintenance should be conducted according to the stipulations in clause 6 and charging should be carried out.
Use, maintenance and charge of the storage batteries
Operation before batteries charged
This stacker is equipped with a fixed charger. And other built-in chargers are also optional. Insert it into the electric door lock. Insert the power plug of the charger into the socket of the stacker or connect it to the battery case. Turn on the general power switch of the stacker, then plug the charger’s power plug into the AC power. Finally charge the battery. When the batteries are fully charged or have been charged in full, the charger will automatically stop charging. (Please refer to the manual of charger for details). When a charger is inserted into the electric lock, insert the power plug into the socket of the battery case or charger. Then plug the charger’s power plug into the AC power. Finally charge the battery. After the batteries are fully charged, the charger will automatically stop charging.
Warning: There is hydrogen gas accumulated in the battery case during charging. Thus the charging environment requires good ventilation and there shall be no flame, otherwise explosion or fire may occur.
Initial charge: Initial charge should be conducted for batteries that have never been used.
Use and maintenance
- In order to guarantee the service life of the batteries, the batteries in use should be fully charged. Insufficiently charged batteries must not be used. During the process of use, close attention should be paid to the discharge current. Over discharge is prohibited.
- The batteries in normal use should be over-charge, but over-charge must be properly conducted for the batteries in following situations, i.e. equalizing charge. a. The “lag-behind” batteries--batteries with a voltage lower than that of the other batteries in the series connected process and the batteries having been repaired for failure. Equalizing charge should be conducted with the positive and negative ends of the “lag-behind” series connected with the positive and negative ends of the charge, the DC power supply, and the charge should be conducted independently. b. Equalizing charge should be conducted for the batteries in normal use every 2-3 months. c. Equalizing charge should be conducted for the batteries that have not been used for a long period of time before use.
Storage: Batteries should be stored in a clean, dry and well ventilated warehouse with a temperature of 5-40°C. The valid shelf life is 2 years. The batteries should be kept according to the following requirements: a. Do not short circuit the ends of batteries. b. Avoid contacting with any harmful substances. No metallic matters are allowed to drop into the battery cases. c. The batteries should not be placed upright down and should not be lifted by the pole.
Charger: If the charger you use is full automatic type. It must meet with the following 2 requirements:
- The output voltage of charger: 24V
- The output current of charger: 30A
Inspection before operation
For the sake of safety operation and good situation of the electric truck, it is compulsory to check the truck completely before operation. Contact the sales department of our company when founding problems.
Check point and check content
No. | Check point | Check content |
---|---|---|
1 | Braking system | Operation handle When the operation handle is turned, with the handle switching between area A and B, there is a noise from the brake. |
2 | Braking system | Brake clearance The clearance between brake shoes should be kept between 0.2mm and 0.8mm. |
3 | Steering system | Operation handle Degree of tightness and rotary flexibility. |
4 | Steering system | Oil pipe Leakage or not. |
5 | Wheels | Hydraulic oil Appropriate oil quality. |
6 | Wheels | Lifting oil cylinder Whether there is any oil leakage. |
7 | Wheels | Pins, screws and all the fasteners Check all the fasteners of the truck’s wheels, i.e. pins or screws, loose or not. |
8 | Wheels | Wearing status Compare the diameter of wheels with the original, when its diameter reduces by 5%. |
9 | Storage battery | Charge Confirm the display state of the battery-charger. |
10 | Storage battery | Electrolyte The solution level and density of electrolyte. |
11 | Horn | Connecting line The connecting line and socket shall be firm. |
12 | Horn | Horn Press down the horn button to check whether the horn sounds. |
13 | Instrument | Function Check whether the instrument displays normally or not. |
14 | Others | Function Check that whether lifting, lowering, forward and backward movement and emergency reverse of the truck is normal, and if there is any abnormal noise. |
Sovans Electric Pallet Stacker CTD10R-E Description
The Sovans Electric Pallet Stacker CTD10R-E is built for durability and reliability, with a robust steel frame and high-quality components. The adjustable fork length and 120-degree steering make it incredibly versatile, perfect for navigating tight spaces and handling various load sizes. The powerful 24V battery ensures long-lasting performance, while the built-in charger simplifies recharging. The CTD10R-E also boasts an intuitive control panel, making it easy for operators to manage speed, direction, and other functions.
Inspection after operation
After operation, the smog on truck shall be wiped out. Besides, the following check shall be carried out: Keep visibility of all graphics contents marks such as warning signs, nameplates and notice board. These marks are able to intact, enough and warn the operator to some degree. The situation about deformation, distortion, damage or breakage Add lubrication and grease if necessary. Replace faulty components.
Periodic Maintenance and Repair
Comprehensive check for the truck can avoid malfunction and ensure the service life. The hours listed in maintenance procedures are based on the cases that the truck works for 8 hours per day and 200 hours per month. For the sake of safety, maintenance shall be carried out according to the maintenance procedure.
Notice
All the repair work shall be carried out by professional personnel. Please contact the sales department of our company if you need to adjust or replace the components.
9.1 Precautions During Maintenance
Notice
The components for replacement shall be produced completely by our company. When replacing components of the truck, the components with the same safety requirement as the original design shall be used. The lubricating oil and hydraulic oil in use shall be recommended by our company.
(1) Places for Maintenance:
Notice
The places for maintenance shall be appointed and can provide other services such as hoisting and safety protection facility, etc. The places shall have level ground and good ventilation. The places shall be equipped with fire-extinguishing devices.
Before Service Maintenance Matters Needing Attention:
Notice
- No smoking.
- Arrange the self-protection work.
- Wipe out the effusive oil in time.
- Before adding lubricating oil, clean up the dirty oil or dust on the joint with a brush or cloth.
- Except in certain situations, turn off the key switch and pull off the power socket.
- Lower down the fork arms to the lowest point when carrying out maintenance.
- Ensure no goods on the truck when demounting the high-pressure oil pipe. Besides, the fork arms shall be descended to the lowest position; by this way, the pressure of the hydraulic system can be released.
- For the reason that there are capacitors storing a little amount of electric energy in the circuit, before contacting the binding post of the main circuit, discharge at first.
- Clean the electric section with compressed air, never flush with water.
- When the truck requires high-position maintenance, altitude safety protection must be carried out for the repairing and maintenance personnel.
Inspection and Maintenance Before the New Truck is Put Into Operation
In order to follow the industry-related regulations and ensure the absolute security of the truck in transportation, for new ex-factory trucks, it is possible that there is no electrolyte inside the storage battery before the first use (except for inland sale). The electrolyte of the storage battery is prepared well before the truck leaves the factory, and it is filled into the storage battery by professional personnel before the first use. First, place the truck in a site with good ventilation, open the lid of the storage battery box, and open all the top plastic lids of the storage battery. The plastic pot with storage battery electrolyte inside is raised using a plastic funnel, and the electrolyte is poured into the storage battery in a slow way until the liquid level can be seen. After all the storage battery is filled, conduct an initial charge to the storage battery timely according to the operation requirements of initial charge 5.1.
Daily Inspection
Inspection of hydraulic oil level: lower the fork to the lowest position, and oil charge is 12L. Recommendatory trademark for the hydraulic oil should be chosen. Check the capacity of storage battery: refer to the use and maintenance of storage battery.
The inspection according to the need
- Clean the truck
- Inspect and screw down each fastener
- Inspect the damage state of wheels
The inspection and maintenance after 50 hours (Weekly) Braking system
- When the operation handle is turned, with the steering handle switching between area A and B, there is a noise from the brake.
- The oil dirt and dust on the turning gearwheel should be cleaned.
- The clearance between brakes should be kept between 0.2mm and 0.8mm.
Capability of electrolyte - Inspect the liquid level of electrolyte, pure water can be used for supplement if the liquid level is too low.
- The specific gravity should be 1.28g/ml after charged.
Density of electrolyte - Cover the lid, and flush with tap water.
Clean the storage battery - Burnish the coarse surface of contacts using sandpaper.
The inspection and maintenance after 200 hours (Monthly)
Besides the weekly maintenance, the following maintenance should be carried out, and when the parts must be adjusted and replaced, please contact with maintenance personnel of our company. (keep monthly maintenance record)
Check Point | Check Content |
---|---|
Whole Status | Abnormal or not |
Horn | Sound |
Operation Handle | When the operation handle is turned, with the handle switching between area A and B, there is a noise from the brake. |
Brake Clearance | The clearance between brakes should be kept between 0.2mm and 0.8mm. |
Operation Handle | Degree of tightness and rotary flexibility |
Truck Frame and Fastener | Function, and check cracks, lubrication and tightness of fasteners |
Connecting Rod and Wheel Carrier | Function and check the cracks, bending, deformation and lubrication condition |
Oil Pipe | Whether oil pipes leak or not |
Hydraulic Oil | Proper quantity of oil |
Lifting Oil Cylinder | Whether there is any oil leakage or not |
Electrolyte | Liquid level, specific gravity and cleanness |
Plug | Function, whether it is damaged or not |
Key Switch | Function |
Contactor | Contact performance and function |
Inching Switch | Function |
Controller | Function |
Driving Motor | Wearing status of carbon brush and selenium rectifier |
Lifting Motor | Wearing status of carbon brush and selenium rectifier |
Steering Motor | Wearing status of carbon brush and selenium rectifier |
Fuse | Whether it is perfect or not |
Wiring Harness and Clearance Terminals | Whether flexible and whether damaged or not |
Adjustment of the brake clearance
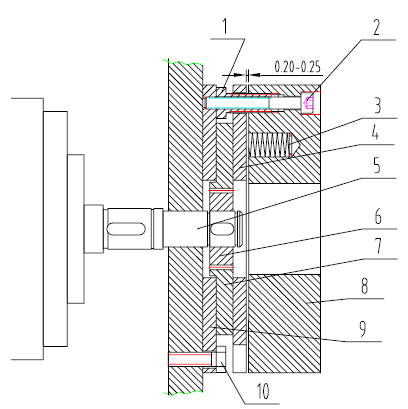
- Hollow screw
- Fitting screw
- Spring
- Armature
- Motor shaft
- Spline housing
- Friction plate
- Electromagnetic coil
- Mounting cover plate
- Mounting screw
The structure of brake is shown as the figure. After a period of use, performance of the brake will decline due to the wearing and tearing of the brake plate. Then it is necessary to adjust the clearance of the brake. As indicated in the drawing, first use the insert ruler to check the clearance between the brake plate and magnetic steel. If the clearance is over 0.5mm, adjust it. Before the adjustment, clean the dirt and dust on the friction plate. During adjustment, first loosen the fitting screw.
Then adjust the length of the adjustment screws 1 and screw down the tightening screws. After the adjustment, the clearance between brake plate and magnetic steel shall be kept between 0.2-0.3mm. During the adjustment, make sure that the three tightening screws are adjusted evenly so as to ensure that the clearance between brake plate and magnetic steel are distributed around equally. After the adjustment, turn on the brake with 24V DC power. Then the brake will make clear sound.
Maintenance for 600 hours (every three months)
During the maintenance every three months, the monthly maintenance process shall be repeated. When the parts must be adjusted and replaced, please contact with maintenance personnel of our company.
Component | Maintenance Content |
---|---|
Contactor | Burnish the coarse surface of contacts using sandpaper. Replace according to the status when the function is not well. |
Motor | Wearing status of carbon brush and selenium rectifier. |
Brake | Clean the dirt and dust on friction plates of the brake, meanwhile check the wearing status of the friction plates. |
Maintenance for 1200 hours (every six months)
During the maintenance for a half year, the maintenance process for three months shall be repeated. When the parts must be adjusted and replaced, please contact with maintenance personnel of our company.
Component | Maintenance Content |
---|---|
Contactor | Burnish the coarse surface of contacts using sandpaper. Replace according to the status when the function is not well. |
Motor | Wearing status of carbon brush and selenium rectifier. |
Decelerate Box | Replace the gear oil |
Oil Filter | Clean |
Brake | Clean the dirt and dust on friction plates of the brake, meanwhile check the wearing status of the friction plates. |
Hydraulic System | Replace hydraulic oil. Check if there is any leakage in the lifting cylinder and replace the seals when necessary. |
Fork Wheel and Bearings | Check the wearing condition, and replace them if necessary |
Recommended working medium
- Hydraulic oil: A. When it is normally loaded, we advise: Hydraulic oil: LHP150VG46, in accordance with standard DIN51524T.2, the average sustained temperature should between 40 degrees to 60 degrees. B. When it is over loaded, we advise: Hydraulic oil: LHP150VG68, in accordance with standard DIN51524T.2, the average sustained temperature is above 60 degrees. C. When it is lightly loaded with low temperature, we advise: Hydraulic oil: HLP150VG32, in accordance with standard DIN51524T.2, the average sustained temperature is below 60 degrees. D. At the occasion with variable loading, we advise: All the working conditions mentioned above can use the hydraulic oil LHP150VG46 in accordance with standard DIN51524T.2 for replacement. The viscosity of this lubricant is very high (mostly used hydraulic oil). If it is difficult to buy hydraulic oil, SAE20W/20 engine oil can be used to substitute HLP68 hydraulic oil.
- Gear oil: Hyperbola gear oil 85W-90(GL-5)
- Lubricating grease: Lithium grease of type 3 All kinds of depleted hydraulic oil, gear oil and grease will pollute the environment. For this reason, recycle the replaced working medium or treat according to local pertinent regulations.
Maintenance period of consumables and partial parts
Items | Maintenance content | Maintenance period | Remarks |
---|---|---|---|
Bearings of fork wheel | Replacement | 1200 hours | |
Fork wheel | Replacement | 1200 hours | |
Seals | Replacement | 1200 hours | Replace when finding out damage |
Gear box | Replacing lubricant grease | 1000 hours | |
Hydraulic oil | Replacement | 1000 hours | |
High pressure oil pipe | Replacement | 2000 hours | Replace when finding out damage |
Strainer of hydraulic reservoir | Cleaning | 1000 hours | |
Driving motor | Check for carbon brushes and bearings | 1000 hours | |
Steering motor | Check for carbon brushes and bearings | 1000 hours | |
Oil pump motor | Check for carbon brushes and bearings | 1000 hours |
The store, transportation and loading of truck
The store of truck: If the electric pallet stacker is not used for over two months, it should be placed in the room which is in good ventilation, no frost, clean and dry; also the following measures should be taken:
- Clean the truck thoroughly.
- Lift the forks completely for several times, check it is normal or not.
- Lower the forks to the lowest position.
Support the side near to the driver of the truck with square timber to lift the driving wheels of the truck from the ground.
- Apply a layer of flimsy oil or grease on all the bared surface of mechanical parts.
- Lubricate the truck.
- Check the status of storage battery and electrolyte, and imbue the non-aid lubricating grease to the binding post of storage battery.
- All the electrical contacts should be sprayed using appropriate contacts spray.
Transportation of truck: If the truck needs to be transported for a long distance, support the side near to the driver of the truck with square timber to lift the driving wheels of the truck from the ground. The two front wheels of truck shall be fixed stably by sphenoid wood block. Fasten the truck to transport vehicle with ropes.
Loading and unloading of truck: Before loading the truck, check out the nameplate for the total weight of truck to choose appropriate hoisting handling equipment. The hoisting of truck shall be kept level, and landing shall be kept slow and stable. The personnel around shall watch for safety. One of the personnel is responsible for conducting. If the other truck is used for loading and unloading, please watch the bottom situation of the truck. Take care to insert the fork arms to the bottom, in avoidance of damaging the driving wheel, balance wheel and forward wheel.
Replacement of storage battery
The replacement procedure of storage battery is as follows:
- Open the side door of storage battery and take it down.
- Pull down the socket connector of storage battery from the truck.
- Pull out the pin of battery case to loosen the battery.
- Pull out the storage battery from the side way and take the storage battery away with special car or using hoisting method.
- The mounting method of putting the storage battery back into the battery pack is opposite to the above procedures.
Notice Handle the storage battery gently during hoisting and transportation of the battery. Otherwise it will cause damage to the battery or bring danger to human body.
Setup Guide
Follow these steps to operate, assemble, and configure your Sovans Electric Pallet Stacker CTD10R-E:
- Charge the battery fully before the initial use.
- Assemble the pallet stacker according to the user manual, ensuring all screws and bolts are tightly fastened.
- Adjust the fork length to match your load requirements.
- Power on the machine and use the control panel to adjust speed, direction, and other functions.
- Always ensure the load is centered and securely placed before lifting and transporting.
Safety Rules for the User and Driver
To use the motor industrial truck effectively, the following rules are established. Section 14.1 is applied to the user, and section 14.2 is for the driver.
Applied to the User
Users include the owner or the leaser, whether an individual or a corporation.
The Qualification of the Driver
The driver of the motor industrial truck should be trained, pass examination, and obtain the operation qualification.
The truck working in flammable and explosive circumstance
Only the industrial motor truck getting the qualification of the national authoritative department and getting the license of working in the flammable and explosive circumstance, should work in the circumstance. This kind of truck should be marked with proper stamp sign, and the relevant building or the plant should be marked too. The classification of the building or the field condition should agreed on by the user and the national relevant authoritative department.
Passenger
Except for special seats, the vehicle can not carry passengers. The passengers are forbidden to step on the ascent machine or the attachment, except for the following conditions: The truck mounted working platform (except for the high-lift order picker):
- The platform should be fixed on fork rack/ fork firmly.
- If there is no ascent control device, when there is person on the platform, the driver should leave the driving position.
- When there is person standing on the platform with ascent control device, only this ascent control device on the platform can be used.
- The overall weight of the platform, the load and the people should not over the half of the weight marked on the vehicle nameplate.
- The platform on the truck should not be used to transport people. But if for the hand work, the truck can be adjusted for operation in a small range.
Use of the forklift
The change of the capacity and nameplate of the truck
The truck in use shall not exceed the rated capacity stipulated by the factory. Without the permit of the factory, any amendment of the design is forbidden, and should not add any attachment on the truck, in order to prevent the influence of the capacity and operation safety of the truck. Any changing because of adding attachment should not reduce the security and accord to the requirement of this rule. After adopting the attachment, the capacity of the truck, the operation and the repair direction board, label or pattern should be altered correspondently. The user should ensure all the nameplate and label in proper position, and maintain handwriting clear.
Stability
The user should pay attention to section 6 of the code, which is about the stability of the truck in the working conditions. When operating correctly, the high lift truck accord with the section 6 is steady, but the incorrect operating or the wrong maintenance could let the truck working unsteadily. The factors that may influence the stability are: the condition of the ground and the floor, gradient, speed, load, the weight of the storage battery, the dynamic force and the static force as well as the judgment train conditions of the drivers. When the truck is working in the condition differ to the regular working condition stated in the section 6, should reduce the load. When the truck mounted attachment working without load, it should be viewed as partial load.
The protection requirement and protection equipment
The truck should be painted with obvious color differing from the surrounding circumstance. The driving type high-lift truck should be mounted with protection cabane, except for the condition where the load could not drop onto the driver. When convey the load maybe fall to the driver using high-lift truck, should adopt shielding shelf with enough height, weight and the opening size is small enough to prevent the entire load or part of them from falling onto the driver. When it is necessary to denote the working condition, the truck should add caution device, such as light or flash lamp. In the permit of the factory, it is allowed to install turning hand hold on the steering wheel formerly without it.
The transportation and storage of the fuel
The truck should refuel in the stated place. The fuel station should be ventilated, in order to reduce the accumulation of the fuel gas to the least. In opening pit, subway entrance, and lift well or other similar conditions nearby should not fill in the liquefied petroleum gas and replace other dismountable liquefied petroleum gas container. It is forbidden to smoke in the place of refuel, and should alarm using placard. If the liquid fuel is not transport using pipeline, it should be transported using airtight container. Only the personnel trained and appointed can fill or change the liquefied petroleum gas container. When store and transport the liquefied petroleum gas container, should fasten up the filling valve, and the safety valve should connected to the vaporization room directly. When storing the container, should screw the protective cap on the connection mouth. Before filling and/or reusing, should inspect the container to ensure that it is vapor proof. Especially pay attention to the valve and the connective part is vapor proof. The damaged container should not be used. Only the permitted corporation could repair the liquefied petroleum gas container.
The charging and changing of the battery
The battery charging station should set in the appointed area. The charging station should prepare the equipment using for flushing and neutralizing the overflow electrolyte, the fire control device, the measure avoiding the truck damage the charging device and the adequacy ventilation facility blow away the fume off from the battery. In the area of charging, it is forbidden to smoke and alarm with placard. Only the personnel trained and permitted can change or charge the battery. The battery repairing people should wear protective clothes. All the work of changing the battery should carried out according to the description of user’s manual from the factory. When reinstall the battery, should adopt measures to make the battery connecting, orientation and fixation correctly. Do not put tools and other metal substance on the lidless battery. Without the special approval (for example the truck factory), the electrical motor truck should not change the battery with different voltage, weight or size. It is obliged to use the battery stated by the factory. It is obliged to prepare the facility for changing battery safely. When hanging up the battery using hoisting equipment, it is necessary to use insulated steeve. If adopting chain hoist, it is necessary to equip chain box. If adopting chain block, the lidless battery should be covered by a piece of rubber blanket or other insulated materials, to prevent the short circuit of chain and the connecting wire or connecting terminal between the battery lattice.
The invalid or damaged truck
If finding the motor industrial truck existing insecurity factors, it should stop using and give away on the spot. After repairing and recovery to the safety conditions, it can be reused.
Accident
Once the accident happens, for example the staff injures, the truck damages the building or the equipment, firstly should organize salvage, do best to protect the accident field and report to the governor.
Operating conditions
Channel and stacking field
The ground of the operating field should have enough carrying capacity, and it is necessary to maintain it well not to influence the truck operating safely. The transporting channel of the truck should have well visual field, and it is easy to turn, and no grade, steep slope, narrow channel and low roof board. The outline or the borderline must be clear. In the road where it is easy to meet the stepping truck, the width of the channel should be adjusted. Advising the grade of the channel should not over 10%, the top and the bottom of the slope should transit smoothly, to prevent the load vibration or the bottom of the truck from colliding the ground. When the grade is over 10%, installing a sign is advised. If the truck is in operation (transport) and the load block off the sight, when the vehicle is operating, the load should located on the backward of the truck operation direction. For example: in some conditions (for example stacking and climbing), when the vehicle is operating, the load is required on the forward of the vehicle operation direction. Then, the driver should drive the vehicle carefully. It is necessary to attend: if the operation condition require, should equip accessory (assistant) equipment or assistant. The passage, road, runway, floor or slope should maintain good operating conditions, to prevent the truck or the load from being damaged, and to prevent reducing the stability of the vehicle. In dangerous state, including the barrier danger on the top, should mark on the clear location. The fire fighting passage, the upstairs passage and the fire fighting equipment should maintain expedite.
Gangplank or transition board
All the gangplank or transition board should has enough safety coefficients to bear the truck with load. On the gangplank or transition board should marked the max passing load perpetually. The gangplank or transition board should fixed firmly, to prevent the accidental move, vibration or slide. On the gangplank or transition board should equipped handing or other available equipment to the effect of safety transport. On the conditions of possible, should set the fork hole or suspending ear for moving goods. The gangplank or transition board should have non slip finishing. On the both sides of the gangplank or transition board, should mounted the facility to prevent the truck from going over it’s edge. When the gangplank or transition board is fixed its location, should adopt measures to prevent the reverse joint truck from moving suddenly.
Lighting
When the photometric brightness on the operating field is less than 32LX, the vehicle should equipped auxiliary light.
The suspending of the truck
The sling should be tied to the lifting spot which the factory appointed.
The synchronizing operation of the truck
Conveying bulky or heavy load using two trucks simultaneously is a dangerous operating which requires special care. And this kind of conditions should be taken as special conditions and carried out under the supervision of the operator responsible for operation.
Elevator (lifter)
The elevator (lifter) for transporting the industrial truck can bear the overall weight of truck, load and the drivers. This kind of elevator (lifter) must be appointed, and the drivers should use the appointed elevator (lifter).
Operating on the road vehicle (trailer) and rail vehicle
Before the motor industrial truck drive to the road, the road vehicle should apply the brake and wedging to prevent moving. Exception: the road vehicle equipped with automatic snap lock type parking brake can not use the wedge. The industrial motor truck passing in and out without connect to the tractor, to prevent the semi trailer hold up can use support It is necessary to build up the operating communication and operating order, to prevent the rail vehicle move accidentally when downloading. The road vehicle (trailer) and rail vehicle should endure the overall weight of vehicle, load and the drivers. It is necessary to inspect if the pavement is crushing, having holes or other damage. When the industrial truck is operating at high place or platform, should not use the industrial truck to move other vehicles. Never open the door of the rail truck using industrial truck; expect for equipped with special device and the driver has passed the train to use the device.
Applied to the driver
The safety operating of the industrial truck lies on the control manner of the driver ro a considerable degree. The safety rules applied to the drives are as follows:
- general rule;
- transporting (lifting and stacking) rule;
- operating (driving) rule;
- the rule for the driver maintaining the truck. Without regard to the rules maybe conduce:
- the serious danger of damaging the driver or other personnel;
- Damage the materials.
General rule
Only the personnel who have been trained and get the qualification of operation are permitted to drive the industrial truck. The motor industrial truck could not carry passengers, except for equipped with the facility for the passengers sitting. The driver should pay special attention to the operating circumstance, including the person nearby other staves and fixed or moving substances, and it is necessary to watch out for the passerby at any moment. No matter whether there is load on the lifting part of the truck, it is forbidden anyone passing or standing under the lifting part of the truck. If the people, building, organization or equipment accident happens, it is necessary to report to the relevant officer at once. The driver should not change, add or demolish the truck components without the permission to influence the performance of the truck .It is not allowed to install accessorial frame or handle on the steering wheel ,except the factory has installed it. The driver should use the truck in the using range. When operating high stacking job, convey high and multi piece piled goods using driving type high-lift truck, it is necessary to use the truck with blind goods shelf and canopy guard shelf. Exception: if there is no danger of the load fall down on the driver, the truck without blind goods shelf can be used. When operating high stacking job, convey high and multi-piece piled goods using walking type truck, the blind goods shelf is necessary.
Load carriage (lifting and stacking) rule
Load
The industrial truck or the combination of the industrial truck and attachment only can convey the load not over its rated load weight. The capacity of the industrial truck with attachment maybe less than the one marked on the nameplate. Any measure of enhancing the capacity of the truck is forbidden, for example the adding people or balance weight. In any conditions, especially when using the attachment, it is necessary to pay attention to the operation, location, fixation and transportation of the load. The truck with attachment when unloaded should be treated as with some capacity. Only the rank stabilized or safety load can be conveyed, especially when convey the super long or high load, should pay special care. When convey the load which center of gravity is uncertain, operating the vehicle should special carefully.
The loading and unloading of goods
When loading the goods with forks: A) The space between the forks should fit the width of the conveying load. B) The fork should insert into the inner of the load as deep as possible. But pay attention to not make the fork tip touch the substance except the load. Then the fork should lift to the enough height to move the goods. C) When conveying high and multi-piece piled goods, it is necessary to tilt the mast back ward a little (if can tilt back) to stabilize the load, and should be careful specially. When unloading the goods, it is necessary to descend carefully. If possible, tilt the mast forward a little (or limited)in order to put ready the load and draw out the fork.
Stacking
When stacking, the mast should tilt backward to ensure the stability of the load, approach the goods pile slowly. When the truck approach and face to the goods pile, it is necessary to adjust the mast to the vertical location, and lift the load a little higher than the height of the pile. Then running backward the truck Or if using reach truck, extense the fork and descend it to unload the goods After lifting, start the vehicle, no matter with or without load, it is necessary to operate the brake carefully and placidly. It is necessary to ensure that the stacking is firm. After stacking, draw off the fork, and lower the fork to the operating height. After confirm there is no block on the road, drive away the truck. As for truck can tilt backward , it is necessary to use this function to stabilize the load.
Troubleshooting Guide
No. | Fault | Possible Causes | Troubleshooting |
---|---|---|---|
1 | The stacker cannot start (The contactor does not work either) | ① The fuse of the control circuit is burnt out. | Replace |
② The power switch is in poor connection or is damaged. | Repair or replace | ||
③ The fuse of the main circuit is blown. | Replace | ||
④ The switch of the electric lock is in poor connection or damaged. | Repair or replace | ||
⑤ The connection of the storage batteries is loose or has fallen off. | Tighten | ||
2 | The stacker cannot start (The contactor works) | ① The side magnetic brake of the drive wheel does not suck and the stacker is in a braked condition. | Repair or replace |
② The walking motor carbon brush is worn or there is bad contact between the steering device and the carbon brush. | Repair or replace | ||
③ The magnet exciting coil of the stepper motor is broken or there is bad contact at the wire end. | Repair or replace | ||
④ Bad contact. | Repair or replace | ||
⑤ There is trouble in the MOSFET tube-type circuit board. | Repair or replace | ||
3 | The stacker can only move forward or backward | ① The contactor is in poor connection or burnt out. | Repair or replace |
② There is a malfunction in the circuit board. | Repair or replace | ||
4 | The stacker cannot stop during traveling | Broken contact. The moving contact cannot be reset. | Cut off the power at once and replace the contact |
5 | The brake does not work | ① The erection bolt of the fine motion switch is loose or damaged. | Adjust or tighten the bolt or replace the fine motion switch. |
② The connecting wire of the side magnet brake is loose or damaged. | Tighten the bolt or repair the side magnet brake. | ||
③ The braking plates of the side magnet brake are worn. | Replace the braking plates. | ||
6 | The steering has got stuck | ① The bearing of the steering device is damaged. | Replace the bearing |
② The bearing of the steering device lacks lubricant or there is too much dust. | Clean the bearing | ||
7 | Difficult steering of the drive wheel, noise, and the motor is overloaded | ① The gear or bearing has got stuck because of foreign matters. | Clean or replace the bearing |
② There is a gap in the bearing installed. | Adjust the clearance | ||
③ The front wheel bearing is damaged. | Replace the bearing | ||
8 | The forks cannot be lifted | ① Overload | Reduce the load |
② The pressure of the overflow valve is too low. | Adjust the pressure higher | ||
③ Internal abnormal leakage in the lifting oil cylinder. | Replace the seals | ||
④ Insufficient hydraulic oil. | Add appropriate quantity of filtered hydraulic oil | ||
⑤ Insufficient voltage of the storage battery. | Charge the battery | ||
⑥ The control handle is not horizontal or vertical, the oil pump motor has not been turned on. | Improper operation | ||
⑦ Damaged oil pump motor. | Repair or replace | ||
⑧ Damaged oil pump. | Repair or replace | ||
⑨ Damaged lifting button. | Repair or replace | ||
⑩ The electric lock is not unlocked or is damaged. | Repair or replace | ||
⑪ Seriously insufficient voltage in the cell. | Recharge | ||
9 | The forks cannot be lowered after being lifted | ① The internal mast is overloaded and deformed. | Repair or replace |
② The external mast is overloaded and deformed. | Repair or replace | ||
③ Dead mast roller. | Repair or adjust | ||
④ Mast guiding rod is curved. | Repair or straighten | ||
⑤ The oil return hole is blocked. | Clean | ||
⑥ The electromagnetic valve is out of control. | Shoot the trouble | ||
10 | Reduced end voltage of the storage battery (after charged) | ① Damage of individual battery. | Repair or replace |
② Low level of the electrolytic solution. | Add electrolytic solution | ||
③ Foreign matters in the electrolytic solution. | Replace the electrolytic solution | ||
11 | The truck shakes while traveling | ① Driving wheel locating nuts loosen or come off. | Screw down the locating nuts. |
② The balance wheel, driving wheel, and the two front wheels are not in the same plane. | Adjust bolts on the balance wheel to make the four wheels in the same plane. |
Adjustment Methods of Safety Valve Pressure
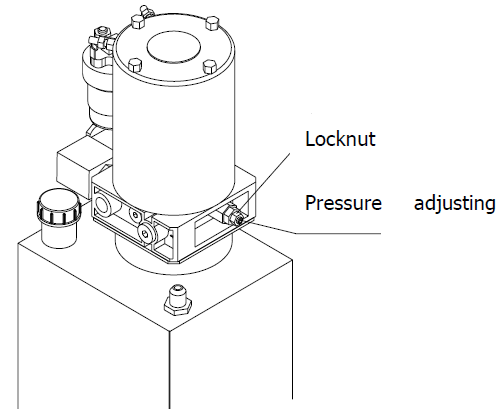
The pressure of safety valves has already been adjusted when the truck is ex-factory. Users shall not adjust the pressure at will, as it can bring danger to the truck’s hydraulic system and safety. If the oil pressure is not in accordance with the specified value, please ask professional personnel to adjust according to the test methods stipulated in the JB/T3300 standards as well as the following methods:
- Screw out the high-pressure oil tube and install a pressure meter with a capacity over 20Mpa at the high-pressure oil outlet.
- Press the lifting operation button to measure the system pressure. The stipulated system pressure is 16Mpa for a truck with a rated load of 1500KG and 16.5Mpa for a truck with a rated load of 2000KG.
- If the oil pressure is not in accordance with the specified value, please loosen the locknuts of the overflow valves. Turn the pressure screw left or right until the pressure reaches the specified value. When the screw is turned clockwise, the system pressure increases. When the screw is turned counter-clockwise, the system pressure decreases.
- After the adjustment, please screw down the locknuts.
Common fault signal & Troubleshooting
NO | Programmer Display Code | Fault | Troubleshooting |
---|---|---|---|
1 | BATTERY DISCONNECT FAULT 4.5 | The battery is not connected | 1) The battery is not connected<br>2) Poor contact in the battery terminals |
2 | BRAKE OFF FAULT 3.4 | Close brake failure | 1) Electromagnetic brake coil is short circuit<br>2) Electromagnetic brake driving is open circuit |
3 | BRAKE ON FAULT 3.2 | Brake failure to open | 1) Electromagnetic brake driving is open circuit<br>2) Electromagnetic brake coil is short circuit |
4 | CURRENTSENSE FAULT 4.1 | Current detection fault | 1) Motor or motor wiring shorted<br>2) Controller fault |
5 | EEPROM CHECKSUM FAULT 4.3 | EEPROM fault | 1) EEPROM Failure or malfunction |
6 | HARDWARE FAILSAFE 4.2 | Over voltage of motor | 1) Motor voltage does not match the accelerator input<br>2) Motor or motor wiring shorted<br>3) Controller fault |
7 | HPD FAULT 3.5 | HPD fault | 1) Accelerator, key switch, or prohibit the importation of several actions to implement operations in the wrong order<br>2) Adjust the accelerator improperly |
8 | MAIN FAULT 2.3 | Main contactor fault | 1) Main contactor is adhesive or open circuit<br>2) The main contactor coil driver error |
9 | MAIN OFF FAULT 2.1 | Main contactor coil driver turn off fault | 1) Turn on the main contactor improperly |
10 | MAIN ON FAULT 2.4 | Main contactor coil driver turn on fault | 1) Turn off the main contactor improperly |
11 | OVERVOLTAGE FAULT 1.5 | Over voltage of battery | 1) Voltage >31V<br>2) Still connected to the charger when the vehicle is running<br>3) Poor contact |
12 | PRECHARGE FAULT 3.3 | Precharging fault | 1) Controller fault<br>2) Low voltage |
13 | SPEED POT FAULT 1.3 | Speed potentiometer fault | 1) Speed potentiometer wiring is open circuit or short circuit<br>2) Speed potentiometer is open circuit |
14 | THERMAL FAULT 1.1 | Over / under temperature cut off | 1) Temperature >80C or <10C<br>2) Overload<br>3) Drive in extremely harsh environments<br>4) Electromagnetic brake does not release normally |
15 | THROTTLE FAULT 1.2 | Over voltage of potentiometer | 1) Accelerator input is open or short circuit<br>2) Potentiometer fault of accelerator<br>3) Choosing the wrong type of accelerator |
16 | UNDERVOLTAGE FAULT 1.4 | Low battery voltage | 1) Battery voltage <17V<br>2) Poor contact of battery or accelerator |
17 | WIRING FAULT 3.1 | HPD fault time is over ten seconds | 1) Incorrect operation of accelerator<br>2) Faults happened in terminal or the mechanical part of accelerator |
Pros & Cons
Pros
- High load capacity (1000 kg)
- Adjustable fork length
- Ergonomic design
- Long-lasting battery
- 120-degree steering
Cons
- Higher price point compared to manual pallet stackers
- Requires regular maintenance
Customer Reviews about Sovans Electric Pallet Stacker CTD10R-E
Customers appreciate the CTD10R-E's durability, versatility, and ease of use. Common compliments include:
- Impressive load capacity
- User-friendly control panel
- Easy assembly and maintenance
- Compact design for navigating tight spaces
However, some users have noted the higher price point and required maintenance as potential drawbacks.
Faqs
What type of battery does the Sovans Electric Pallet Stacker CTD10R-E use, and what are its specifications?
Can the Sovans Electric Pallet Stacker CTD10R-E be used outdoors?
How long does the battery last on a single charge Sovans Electric Pallet Stacker CTD10R-E?
What is the recommended maintenance schedule for the Sovans Electric Pallet Stacker CTD10R-E?
How long does it take to fully charge the battery of the Sovans Electric Pallet Stacker CTD10R-E?
What is the average operating time on a full charge for the Sovans Electric Pallet Stacker CTD10R-E?
Can the Sovans Electric Pallet Stacker CTD10R-E be used on inclined surfaces?
What is the warranty on the Sovans Electric Pallet Stacker CTD10R-E?
How should the Sovans Electric Pallet Stacker CTD10R-E be maintained?
What type of hydraulic oil is recommended for the Sovans Electric Pallet Stacker CTD10R-E?
Leave a Comment