Ruitech Solutions T86 Closed Loop Stepper Driver User Manual
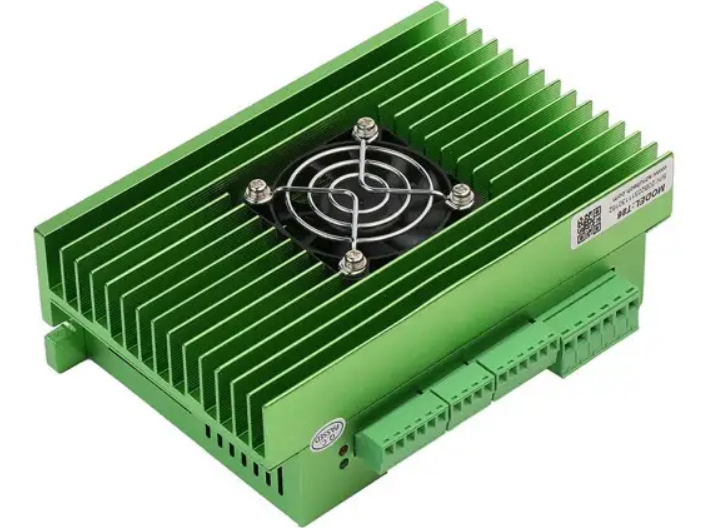
Content
Introduction
Ruitech Solutions introduces the T86 Closed Loop Stepper Driver, a powerful and versatile solution for controlling stepper motors and servos. This driver is designed to provide precise motor control, making it ideal for various applications, including CNC machines, 3D printers, and robotic systems. The T86 is competitively priced, with an estimated price range of $50 to $60, and is currently available for purchase. Its expected launch date is in mid-April 2023.
Detailed Specifications
The Ruitech Solutions T86 Closed Loop Stepper Driver the following key features:
- Compatible with both stepper motors and servos
- Supports various motor control modes, such as step/direction, pulse width modulation (PWM), and quadrature encoder
- Up to 4A per phase current rating
- Built-in thermal protection to prevent overheating
- Communication interfaces: UART, I2C, and SPI
- Protection features: overvoltage, undervoltage, overcurrent, and short-circuit
- Expansion port for connecting additional drivers or accessories
- Compact size and lightweight for easy integration
Product overview
Stepper servo is a stepper motor scheme formed based on the common open-loop stepper motor in combination with position feedback and servo algorithm, which features high speed, high torque, high precision, low vibration, low heating and no loss of step. Based on TI’s new 32-bit DSP processing chip platform, T series stepper servo driver uses the field-oriented control (FOC) and vector field-weakening control algorithm in the servo driver, which has the performance of surpassing the ordinary stepper in all aspects.
The built-in PID parameter adjustment function makes the motor better meet the application of different kinds of loads.
The built-in field-weakening control algorithm makes the motor to reduce the magnetic field characteristics and keep the power at high speed.
The built-in current vector control function makes the motor have the current characteristic of servo and low heating.
The built-in micro-stepping command algorithm makes the motor can run while maintaining a stable and low vibration at various speeds.
The encoder feedback with the built-in 4000 pulse resolution makes the positioning precision increase and never loses the step.
In conclusion, the servo control scheme combined with the characteristics of the stepper motor enables the T series stepper servo driver to better exert the performance of the stepper motor, which can replace the servo application of the same power. It is a new choice of optimal cost performance for automation equipment.
T86-IO driver can set subdivision and other parameters through DIP switch and debugging software. It has protection functions such as voltage, current, and position, and adds alarm output interface. Its input and output control signals are optically isolated.
Power supply | 20 - 80 VAC / 24 – 100VDC |
Control precision | 4000 Pulse/r |
Pulse mode | Direction &pulse, CW/CCW doublepulse |
Current control | Servo vectorcontrol algorithm |
Micro-stepping settings | DIP switch setting, or debugging software setting |
Speed range | Conventional 1200 ~ 1500rpm, up to 4000rpm |
Resonance suppression | Automatically calculate the resonance pointand inhibit the IF vibration |
PID parameter adjustment | Test software to adjustmotor PID characteristics |
Pulse filtering | 2MHz digital signal filter |
Alarm output | Alarm outputof over-current, over-voltage, position error, etc |
We hope that our products with excellent performance can help you to complete the sports control program successfully.
Application environment and installation
Environmental requirement
Item | Rtelligent T86 |
Installation environment | Avoid dust,oil and corrosive environment |
Vibration | 0.5G(4.9m/s2) Max |
Operating temperature/humidity | 0℃ ~ 45℃ / 90% RH or less (no condensation) |
Storage and transportation temperature: | -10℃ ~ 70℃ |
Cooling | Natural cooling/ away fromthe heat source |
Waterproof grade | IP54 |
Driver installation dimensions

Driver installation requirements
Please install the driver vertically or horizontally, with its front-facing forward, top facing upward to facilitate cooling.
During assembly, avoid drillings and other foreign matters falling inside the driver
During assembly, please use M3 screw to fix.
When there is vibration source (such as a driller) close to the installation position, please use a vibrating absorber or a vibration-resistant rubber gasket.
When multiple drivers are installed in the control cabinet, please pay attention to reserve enough space for sufficient heat dissipation. If necessary, you can configure cooling fans to ensure good heat dissipation conditions in the control cabinet.
Description
The Ruitech Solutions T86 Closed Loop Stepper Driver is a high-performance motor driver specifically designed to meet the demands of modern automation systems. It offers a wide range of features, including multiple control modes, high current capacity, and advanced protection mechanisms. The driver's compatibility with both stepper motors and servos adds to its versatility, making it an excellent choice for various applications. The T86's compact size and lightweight design make it easy to integrate into existing systems or new projects. Its robust communication interfaces, such as UART, I2C, and SPI, ensure seamless connectivity with various microcontrollers and single-board computers.
Driver port and connection
Port function description
Function | Grade | Definition | Remarks |
Power supply input | AC | Input AC power supply | AC 20~80V DC 24~100V |
AC | Input AC power supply | ||
Motor connection | A+ | Positive terminal of phase-A winding | Red |
A- | Negative terminal of phase-A winding | Yellow | |
B+ | Positive terminal of phase-B winding | Black | |
B- | Negative terminal of phase-B winding | Green | |
Encoder connection | EB+ | Positive terminal of Encoder phaseB | Green |
EB- | Negative terminal of Encoder phaseB | Yellow | |
EA+ | Positive terminal of Encoder phaseA | Brown | |
EA- | Negative terminal of Encoder phaseA | White | |
VCC | Encoder workingpower 5V positive | Red | |
GND | Encoder workingpower 5V groundterminal | Blue | |
Pulse connection | PUL+ |
Pulse input interface |
3.3 ~ 24V level compatible |
PUL- | |||
DIR+ |
Direction inputinterface | ||
DIR- | |||
Enable terminal | ENA+ |
Enable control interface | |
ENA- | |||
Alarm output | ALM+ |
Alarm output interface |
24V, below 40mA |
ALM- | |||
In place output | Pend+ |
In place output interface | |
Pend- |
Power supply input
The power supply of the driver can be both AC power and DC power, and the input voltage range is 20V~80VAC or 24V~100VDC. Please do not connect to commercial electricity(220VAC) directly!
Power selection reference
Voltage
Stepper motor has the characteristics of torque decrease with the increase of motor speed, and the input voltage will affect the amplitude of high-speed torque reduction. Properly increasing the voltage of the input power supply can increase the output torque of the motor at high speed.
Stepper servo has a higher speed and torque output than ordinary stepper. Therefore, if you want to get better high-speed performance, you need to increase the power supply voltage of the driver.
Current
The working process of the driver is to convert the input high-voltage and low-current power supply into the low-voltage and high-current at both ends of the motor winding. In actual use, the appropriate power supply should be selected according to the motor model, load torque, and other factors.
The effects of regeneration voltage
When the stepper motor is working, it also retains the characteristics of the generator. When decelerating, the kinetic energy accumulated by the load will be converted into electrical energy and superimposed on the driver circuit and input power supply.
Pay attention to the setting of acceleration and deceleration time to protect the driver or power supply.
When the driver is powered off, you will see the driver’s LED indicator on when the load is pulled to make the motor move, which is also affected by this.
Encoder connection
The T86-IO encoder is A/B differential output and is connected in the corresponding order when used.
EB+ | EB- | EA+ | EA- | VCC | GND |
Green | Yellow | Brown | White | Red | Blue |
Rtelligent is equipped with a certain length of encoder cable, Please purchase extension cables of different lengths according to the installation needs.
Motor connection
The matching motor of the T86-IO driver is the corresponding T series stepper servo motor, and its corresponding motor connection order is fixed and unique.

A+ | Red |
A- | Yellow |
B+ | Black |
B- | Green |
Control signal connection
PUL, DIR Port: connection for start and stop command
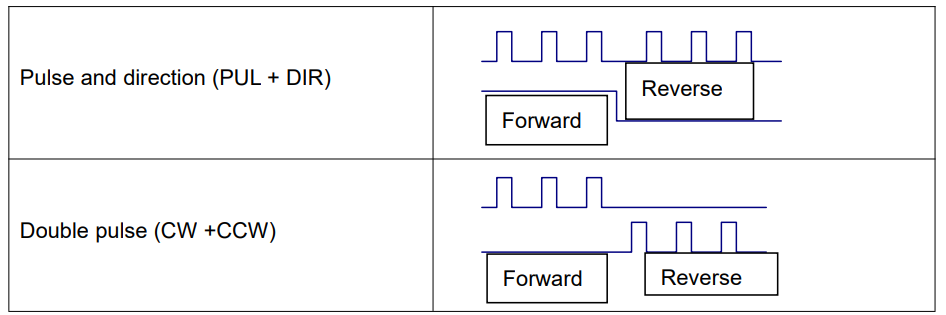
ENA port: enable/disable
When the internal optocoupler is off, the driver outputs current to the motor;
When the internal optocoupler is on, the driver will cut off the current of each phase of the motor to make the motor free, and the step pulse will not be responded.
When the motor is in an error state, it is automatically turned off. The level logic of the enable signal can be set to the opposite.
ALM, Pend port: used for alarm and in place output.
The ALM port is used to output the operating status of the driver to an external control circuit. When the driver is in the error state and the normal working state, ALM outputs different optocoupler levels.
The Pend port is used to output the driver in-place signal. When the difference(position deviation) between the pulse command position sent by the upper computer and the current position of the stepper servo motor is less than the set value, the in-place signal is output. The upper computer receives the signal and confirms that the positioning is complete.
In addition, ALM and Pend ports can be reused as brake control (break) signal through software adjustment, which is used to control the brake switch of stepper servo motor with brake. Since the brake coil is an inductive load, and the coil heating is serious when the motor is running, customers can select special brake controller according to their needs to reduce the brake heating and improve life and reliability.
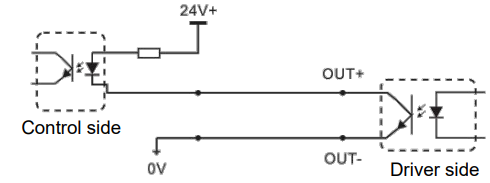
OUT is ALM or Pend, pay attention to connecting current limiting resistor in series
Rtelligent provides solutions for dedicated brake controllers, examples are as follows:
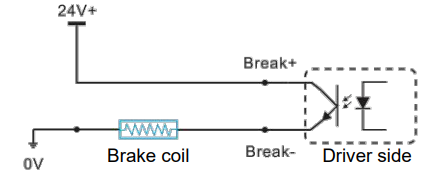
Examples for control signal connection
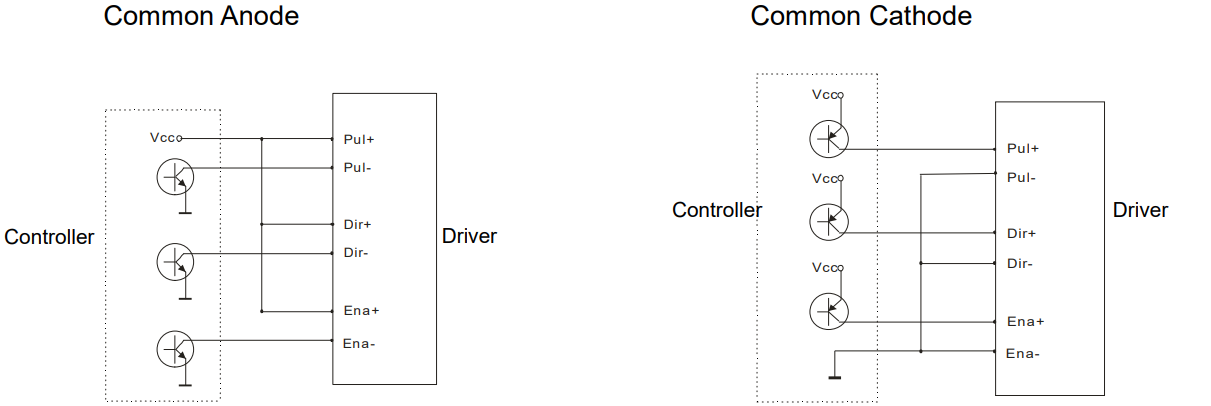
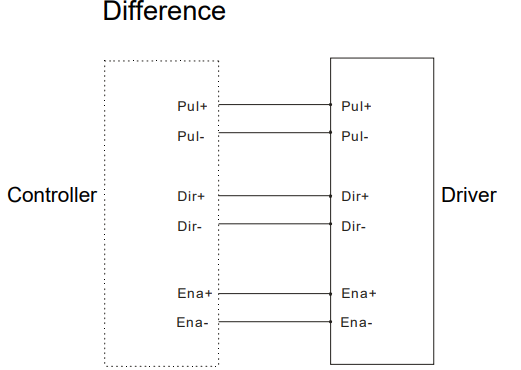
RS232 serial port

S/N | Symbol | Description |
1 | NC |
|
2 | +5V | Positive terminal of power supply |
3 | TxD | RS232 transmitting terminal |
4 | GND | Ground terminal of power supply |
5 | RxD | RS232 receiving terminal |
6 | NC |
|
RS232 serial port is used to connect T86-IO testing software and change other related operating parameters of driver.
Setup Guide
To operate the Ruitech Solutions T86 Closed Loop Stepper Driver, follow these steps:
- Connect the driver to the motor and power supply, ensuring proper polarity.
- Configure the communication settings between the driver and your microcontroller or single-board computer.
- Use the appropriate software libraries and example codes to control the motor's motion and speed.
- Monitor and adjust the driver's settings and parameters through the available interfaces.
The setting of DIP switches and operating parameters
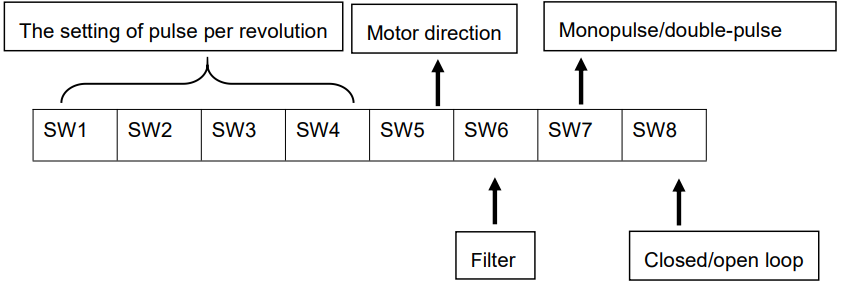
The setting of speed
Steps/revolution | SW1 | SW2 | SW3 | SW4 | Remarks |
3600 | on | on | on | on |
The DIP switch is turned to the “Default” state and the testing software can freely change other subdivisions. |
800 | off | on | on | on | |
1600 | on | off | on | on | |
3200 | off | off | on | on | |
6400 | on | on | off | on | |
12800 | off | on | off | on | |
25600 | on | off | off | on | |
51200 | off | off | off | on | |
1000 | on | on | on | off | |
2000 | off | on | on | off | |
4000 | on | off | on | off | |
5000 | off | off | on | off | |
8000 | on | on | off | off | |
10000 | off | on | off | off | |
20000 | on | off | off | off | |
40000 | off | off | off | off |
DIP SW1, SW2, SW3, SW4 are used to set the pulse per revolution required by the motor.
- Motor speed = command pulse frequency ÷ pulse per revolution
- Motor stroke = number of command pulses ÷ pulse per revolution
Motor direction selection
DIP SW5 is used to set the running direction of the motor under the initial pulse.
- The “off” means that the motor direction is counterclockwise when inputting the initial pulse;
- The “on” means that the motor direction is clockwise when inputting the initial pulse.
The initial pulse is the testing pulse used when developing the driver software; Please refer to the actual running direction of the motor
Pulse filtering function selection
DIP SW6 is used to set the pulse filtering function of driver.
- The “off” means the pulse filtering function is off;
- The “on” means the pulse filtering function is on.
The pulse filtering function is the filtering action by the driver upon the input commands. When the filtering function is on, the driver will smoothen the input pulse command, which can make the motor operation acceleration and deceleration softer, but this will also cause certain delay of the pulse command.
Filtering time setting: The default time of filtering function is 6.4ms, and the software can change the time below the 25.6ms. The set value x50us is equal to the actual time.
Pulse mode selection
DIP SW7 is used to set the pulse command mode of drivers.
- The “off” means pulse + direction (monopulse) mode;
- The “on” means double pulse mode.
Open/closed loop selection
DIP SW8 is used to set the driver control mode.
- The “off” means the closed loop control mode;
- The “on” means the open loop control mode and can be used to test the motor.
Driver working status LED indication
LED status | Driver status | |
![]() | Green indicator is on for long time | Driver not enabled |
![]() | Green indicator is flickering | Driver working normally |
![]() | One green indicator and one red indicator | Driver overcurrent |
![]() | One green indicator and two red indicators | Driver input power overvoltage |
![]() | One green indicator and three red indicators | The internal voltage of the driver is wrong |
![]() | One green and four red indicators | Tracking error exceeds limits |
![]() | One green and five red indicators | Encoder phase error |
Common faults and troubleshooting
Phenomenon | Possible situations | Solutions |
Motor does not work |
Power indicator is off | Check the power supplycircuit for normal power supply |
The motorrotor is lockedbut the motor does not work | Pulse signal is weak; increase the signal current to 7-16mA | |
The speed is too slow | Select the rightmicro-stepping | |
Driver is protected | Solve the alarmand re-power | |
Enable signalproblem | Pull up or disconnect the enable signal | |
Command pulse is incorrect | Check whether the uppercomputer has pulse output | |
The steering of motor is wrong | The rotarydirection of motoris reverse |
Adjust the DIP SW5 |
The motor cable is disconnected | Check the connection | |
The motor has onlyone direction | Pulse mode erroror DIR portdamaged | |
Alarm indicator is on | The motor connection is wrong | Check the motorconnection |
The motorconnection and encoder connection are wrong | Check the sequence of encoder connection | |
The voltage is too high or too low | Check the powersupply | |
The position or speed is wrong |
The signal is disturbed | Eliminate interference for reliable grounding |
The command input is incorrect | Check the upper computer instructions to ensure the output is correct | |
The settingof Pulse per revolution is wrong | Check the DIP switchstatus and correctly connect the switches | |
Encoder signal is abnormal | Replace the motor and contact the manufacturer | |
The driver terminal |
Short circuit between terminals | Check power polarity or external short circuit |
burned up |
Internal resistance between terminals is too large | Check whether there is any solder ball due to excessive addition of solderon the wire connections |
The motor is out of tolerance | Acceleration and deceleration time is too short | Reduce command acceleration or increase driver filtering parameters |
Motor torqueis too low | Select the motorwith high torque | |
The load is too heavy | Check the load weightand quality and adjust the mechanical structure | |
The currentof power supplyis too low |
Replace the appropriate powersupply |
Guarantee Clause
Warranty period: 12 months
We provide quality assurance for one year from the date of delivery and free maintenance service for our products during the warranty period.
Exclude the following:
Improper connection, such as the polarity of the power supply is reversed and insert/pull the motor connection when the power supply is connected.
Beyond electrical and environmental requirements.
Change the internal device without permission.
Maintenance process
For maintenance of products, please follow the procedures shown below:
Contact our customer service staff to get the rework permission.
The written document of the driver failure phenomenon is attached to the goods, as well as the contact information and mailing methods of the sender.
Ruitech Solutions T86 Closed Loop Stepper Driver Pros & Cons
Pros
- Compatible with stepper motors and servos
- Multiple control modes and robust communication interfaces
- Advanced protection features
- Expansion port for connecting additional drivers or accessories
Cons
- Limited to 4A per phase current rating, which may not be sufficient for high-power applications
- Requires a separate power supply
Customer Reviews
Customers generally praise the Ruitech Solutions T86 Closed Loop Stepper Driver for its versatility, ease of use, and robust feature set. The majority of users appreciate its compatibility with both stepper motors and servos, as well as its multiple control modes and communication interfaces. Some users mention that the T86's 4A current rating per phase is sufficient for most of their projects, although those requiring higher current may need to consider alternative solutions.
Faqs
What is the maximum current rating of the T86 Driver?
Can the Servo Driver be used with both stepper motors and servos?
What communication interfaces does the T86 support?
What are the dimensions and weight of the Ruitech Solutions Stepper Servo Driver T86?
Does the Ruitech Solutions Stepper Servo Driver T86 have thermal protection?
How many drivers can be connected to the Ruitech Solutions expansion port?
What is the operating voltage range of the Ruitech?
Can the Ruitech Solutions be controlled using Arduino?
Is the Ruitech Solutions T86 Closed Loop Stepper Driver compatible with Raspberry Pi?
What is the return policy for the Ruitech Solutions?
Leave a Comment